Method and device for measuring angle of flange
A measuring device and edge angle technology, applied in angle/taper measurement and other directions, can solve problems such as accuracy problems
- Summary
- Abstract
- Description
- Claims
- Application Information
AI Technical Summary
Problems solved by technology
Method used
Image
Examples
Embodiment Construction
[0033] As shown in Figures 1, 2, and 3, a straightness measuring device for measuring the angle of the rib is composed of a vertical plate 7 provided with an elastic slot 8 and a vertical horizontal plate 6 to form an elastic hinge type measuring device. 7 is provided with a fixed surface "A" surface, and the horizontal plate 6 is provided with a "B" surface perpendicular to the "A" surface on the vertical plate 7; The "C" surface of the "A" surface; the "A" surface of the vertical plate 7 is provided with two fixed connection screws 1, 2, and the upper "C" surface of the two fixed connection screws is provided with the "B" surface reversed. Two adjusting screws 3, 5 for clockwise fine-tuning, and an adjusting screw 4 for clockwise fine-tuning of the "B" face is arranged between the two adjusting screws 3, 5 on the "C" face.
[0034] The "C" surface on the vertical plate 7 is 1 mm lower than the "A" surface, and the elastic slotted hole 8 is arranged at the intersection of the...
PUM
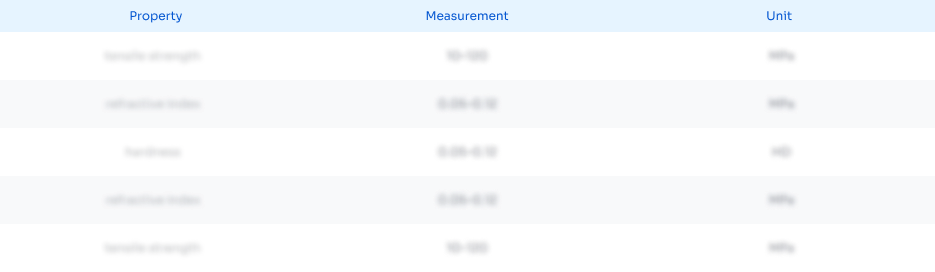
Abstract
Description
Claims
Application Information

- R&D
- Intellectual Property
- Life Sciences
- Materials
- Tech Scout
- Unparalleled Data Quality
- Higher Quality Content
- 60% Fewer Hallucinations
Browse by: Latest US Patents, China's latest patents, Technical Efficacy Thesaurus, Application Domain, Technology Topic, Popular Technical Reports.
© 2025 PatSnap. All rights reserved.Legal|Privacy policy|Modern Slavery Act Transparency Statement|Sitemap|About US| Contact US: help@patsnap.com