Modified alkali lignin ceramic grind-aid dispersing agent and preparation method thereof
A technology of alkali lignin and dispersant, which is applied in the field of modified alkali lignin ceramic grinding aid dispersant and its preparation, can solve the problems of secondary pollution of solid waste and the like, and achieves excellent performance-price ratio, simple process and high efficiency Effect
- Summary
- Abstract
- Description
- Claims
- Application Information
AI Technical Summary
Problems solved by technology
Method used
Examples
Embodiment 1
[0037] Take 100 g of wheatgrass alkali lignin powder and add it to water, adjust the pH value to 10 with NaOH with a mass percentage concentration of 50% under stirring, heat up to 80°C and dissolve it into an aqueous solution with a mass percentage concentration of 40%, add 20 g of sodium sulfite to react for 2 hours; Adjust the pH of the system to 3 with dilute sulfuric acid with a percentage concentration of 20%, add 15g of acrylic acid dropwise, and react at 70°C for 1 hour; then adjust the pH of the system to 12 with NaOH with a concentration of 50% by mass, and add 3g of ammonium persulfate, 8 g of sodium hypophosphite and 8 g of sodium allyl sulfonate were reacted at 85° C. for 5 hours, and a modified alkali lignin ceramic grinding aid and dispersant was obtained after the reaction.
Embodiment 2
[0039] Take 100g of wheatgrass alkali lignin powder and add it to water, adjust the pH value to 9 with NaOH with a mass percentage concentration of 50% under stirring, heat up to 75°C to dissolve into an aqueous solution with a mass percentage concentration of 30%, and add 25g of sodium p-aminobenzenesulfonate React for 2 hours; use dilute sulfuric acid with a concentration of 20% by mass to adjust the pH of the system to 4, add 5g of acrylic acid and 5g of maleic acid dropwise, and react at 80°C for 1.5h; then adjust the pH of the system with NaOH with a concentration of 50% by mass Adjust the value to 11, add 5g of ammonium cerium nitrate, 5g of sodium hypophosphite and 10g of sodium allyl sulfonate, react at 90°C for 3 hours, and obtain a modified alkali lignin ceramic grinding aid dispersant after the reaction.
Embodiment 3
[0041] Take 100g of bamboo pulp alkali lignin powder and add it to water, adjust the pH value to 11 with NaOH with a mass percentage concentration of 50% under stirring, heat up to 85°C to dissolve into an aqueous solution with a mass percentage concentration of 35%, add 15g of sodium metabisulfite and react for 1.5h The pH of the system is adjusted to 3 with dilute sulfuric acid with a concentration of 20% by mass percentage, 20 g of maleic acid is added dropwise, and reacted for 1 h at 75° C.; the pH value of the system is adjusted to 11 with NaOH with a concentration of 50% by mass percentage, and added 3g of ammonium persulfate, 10g of sodium hypophosphite and 6g of sodium allyl sulfonate were reacted at 85°C for 1 hour, and a modified alkali lignin ceramic grinding aid and dispersant was obtained after the reaction.
PUM
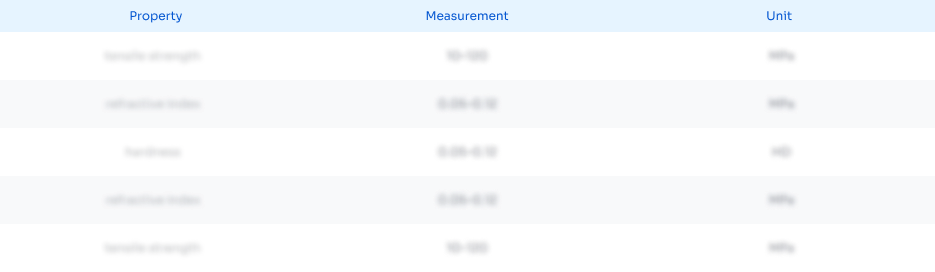
Abstract
Description
Claims
Application Information

- Generate Ideas
- Intellectual Property
- Life Sciences
- Materials
- Tech Scout
- Unparalleled Data Quality
- Higher Quality Content
- 60% Fewer Hallucinations
Browse by: Latest US Patents, China's latest patents, Technical Efficacy Thesaurus, Application Domain, Technology Topic, Popular Technical Reports.
© 2025 PatSnap. All rights reserved.Legal|Privacy policy|Modern Slavery Act Transparency Statement|Sitemap|About US| Contact US: help@patsnap.com