Process for recovering iron and carbon elements from blast furnace gas ash
A technology for recovering blast furnace gas ash and iron, applied in recycling technology, improvement of process efficiency, chemical instruments and methods, etc., can solve the problems of high sorting cost and low process index, and achieve high product quality and technical index advantages , The effect of high removal rate
- Summary
- Abstract
- Description
- Claims
- Application Information
AI Technical Summary
Problems solved by technology
Method used
Image
Examples
Embodiment 1
[0077] 1) Flotation of the gas ash with iron content 31.46%, carbon content 37.90%, -0.071mm particle size percentage by weight and 43.6% weight percentage is directly carried out, and the gas ash is adjusted to a weight concentration of 35% by adding water in the first stirring tank The ore slurry is fed into the second stirring tank, and the flotation reagents, 1050 g / t diesel oil and 215 g / t turpentine oil are sequentially added to the second stirring tank.
[0078] 2) The concentrate from rough flotation is fed to fine flotation. The concentrate from fine flotation is the final carbon concentrate with carbon content of 85.26%, and the carbon recovery rate is 81.55%.
[0079] 3) The coarse flotation tailings and the fine flotation tailings are combined into flotation tailings. The flotation tailings with an iron content of 44.27% and a weight concentration of 45% are fed into the coarse flotation spiral flow cell for heavy selection ,
[0080] 4) The concentrate with 59.2% iron c...
Embodiment 2
[0086] 1) Flotation of the gas ash with iron content of 34.61%, carbon content of 36.84%, and -0.071mm content of 40.2% is directly carried out. The gas ash is added to the first agitating tank to prepare a slurry with a weight concentration of 35%. Two agitating tanks, and adding flotation reagents to the second agitating tank, diesel 985g / t, turpentine 205g / t, and then fed to the rough flotation,
[0087] 2) The concentrate from coarse flotation is fed to fine flotation, and the concentrate from fine flotation is the final carbon concentrate with 84.87% carbon content, and the carbon recovery rate is 81.18%.
[0088] 3) The coarse flotation tailings and the fine flotation tailings are combined to form flotation tailings. The flotation tailings with an iron content of 48.19% and a weight concentration of 43% are fed into the roughing spiral flow trough for heavy selection. ,
[0089] 4) The concentrate with 60.32% of the iron content of the roughing spiral chute is fed into the sel...
Embodiment 3
[0095] 1) Flotation of the gas ash with iron content of 38.23%, carbon content of 33.20%, and -0.071mm content of 46.5% is directly carried out. The gas ash is mixed with water in the first agitation tank to form a slurry with a weight concentration of 33% and fed into the Two agitating tanks, and adding flotation reagents, diesel 960g / t, turpentine 190g / t, into the second agitating tank in turn, feed the crude flotation after adding the chemicals,
[0096] 2) The concentrate from rough flotation is fed to fine flotation, and the concentrate from fine flotation is the final carbon concentrate with carbon content of 85.07%, and the carbon recovery rate is 81.74%.
[0097] 3) The coarse flotation tailings and the fine flotation tailings are combined into flotation tailings. The flotation tailings with an iron content of 49.93% and a weight concentration of 42% are fed into the coarse flotation spiral flow cell for heavy selection ,
[0098] 4) The concentrate with 60.6% iron content i...
PUM
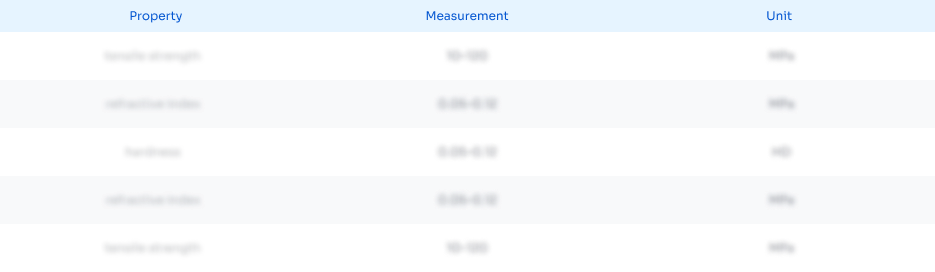
Abstract
Description
Claims
Application Information

- Generate Ideas
- Intellectual Property
- Life Sciences
- Materials
- Tech Scout
- Unparalleled Data Quality
- Higher Quality Content
- 60% Fewer Hallucinations
Browse by: Latest US Patents, China's latest patents, Technical Efficacy Thesaurus, Application Domain, Technology Topic, Popular Technical Reports.
© 2025 PatSnap. All rights reserved.Legal|Privacy policy|Modern Slavery Act Transparency Statement|Sitemap|About US| Contact US: help@patsnap.com