Process for recovering iron and carbon elements from blast furnace gas ash
A technology for recovering blast furnace gas ash and iron, applied in recycling technology, improvement of process efficiency, chemical instruments and methods, etc., can solve the problems of high sorting cost and low process index, and achieve high product quality and technical index advantages , Purification and impurity removal effects are remarkable
- Summary
- Abstract
- Description
- Claims
- Application Information
AI Technical Summary
Problems solved by technology
Method used
Image
Examples
Embodiment 1
[0077] 1) Flotate directly the gas ash with iron content of 31.46%, carbon content of 37.90%, and -0.071mm particle size of 43.6% by weight, and add water to the first stirring tank to adjust the gas ash to a weight concentration of 35%. The ore pulp is fed into the second stirring tank, and flotation reagents are sequentially added to the second stirring tank, diesel oil 1050 g / t, turpentine 215 g / t, after adding the drugs, it is fed into the rough flotation,
[0078] 2) The concentrate from the rough flotation is fed into the fine flotation, and the concentrate from the fine flotation is the final carbon concentrate with a carbon content of 85.26%, and the carbon recovery rate is 81.55%.
[0079] 3) The rough flotation tailings and fine flotation tailings are combined into flotation tailings, and the flotation tailings with an iron content of 44.27% and a weight concentration of 45% are fed into the rougher spiral launder for heavy selection ,
[0080] 4) The concentrate wi...
Embodiment 2
[0086] 1) Flotate the gas ash with iron content of 34.61%, carbon content of 36.84%, and -0.071mm content of 40.2% directly, and add water to the first mixing tank to adjust the gas ash to a slurry with a weight concentration of 35%, and feed it into the second Two stirring tanks, and sequentially add flotation reagents into the second stirring tank, diesel oil 985g / t, turpentine 205g / t, feed into rough flotation after dosing,
[0087] 2) The concentrate from the rough flotation is fed into the fine flotation. The concentrate from the fine flotation is the final carbon concentrate with a carbon content of 84.87%, and the carbon recovery rate is 81.18%.
[0088] 3) The rough flotation tailings and the fine flotation tailings are combined into flotation tailings, and the flotation tailings with an iron content of 48.19% and a weight concentration of 43% are fed into the rougher spiral launder for heavy selection ,
[0089] 4) The concentrate with an iron content of 60.32% in th...
Embodiment 3
[0095] 1) Flotate the gas ash with iron content of 38.23%, carbon content of 33.20%, and -0.071mm content of 46.5% directly, and add water to the first mixing tank to adjust the gas ash to a slurry with a weight concentration of 33%, and feed it into the second Two stirring tanks, and sequentially add flotation reagents to the second stirring tank, diesel oil 960g / t, turpentine 190g / t, feed into rough flotation after dosing,
[0096] 2) The concentrate from the rough flotation is fed into the fine flotation, and the concentrate from the fine flotation is the final carbon concentrate with a carbon content of 85.07%, and the carbon recovery rate is 81.74%.
[0097] 3) The rough flotation tailings and the fine flotation tailings are combined into flotation tailings, and the flotation tailings with an iron content of 49.93% and a weight concentration of 42% are fed into the rougher spiral launder for heavy selection ,
[0098] 4) The concentrate with an iron content of 60.6% in t...
PUM
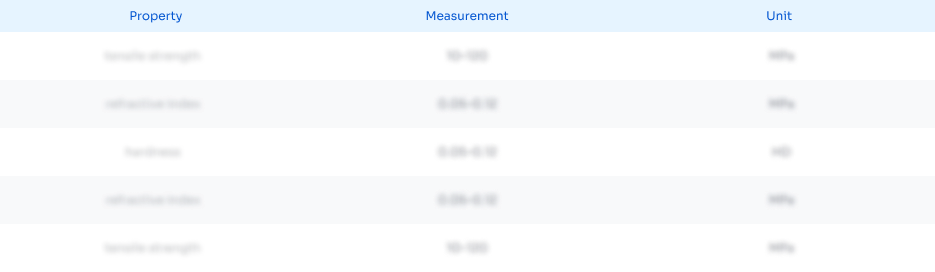
Abstract
Description
Claims
Application Information

- R&D Engineer
- R&D Manager
- IP Professional
- Industry Leading Data Capabilities
- Powerful AI technology
- Patent DNA Extraction
Browse by: Latest US Patents, China's latest patents, Technical Efficacy Thesaurus, Application Domain, Technology Topic, Popular Technical Reports.
© 2024 PatSnap. All rights reserved.Legal|Privacy policy|Modern Slavery Act Transparency Statement|Sitemap|About US| Contact US: help@patsnap.com