Mask plate and mask plate manufacturing method
A manufacturing method and mask plate technology, which are applied in the field of mask plate and mask plate production in photolithography technology, to achieve the effects of improving production efficiency, reducing the number of repeated exposures, and increasing the amount of data collection
- Summary
- Abstract
- Description
- Claims
- Application Information
AI Technical Summary
Problems solved by technology
Method used
Image
Examples
Embodiment Construction
[0050] refer to Figure 4 , the present invention provides a reticle 300 suitable for mask exposure testing. Specifically, the reticle 300 includes: a substrate 301, a plurality of mask components 302 with different thicknesses on one side of the substrate 301, and mask marks 304 on the surface of the mask components 302; The filter film 303.
[0051] The implementation of the present invention will be further described in detail below in conjunction with the drawings and specific embodiments.
[0052] In a specific embodiment, refer to Figure 5, the filter film 303 and the mask part 302 including the mask marks 304 are respectively located on two sides of the substrate 301 . For example, the filter film 303 can be arranged on the surface of the substrate 301 on the light-incident side, and the mask component 302 comprising the mask mark 304 can be arranged on the surface of the substrate 301 on the light-emitting side, wherein the mask mark 304 is located at the same The...
PUM
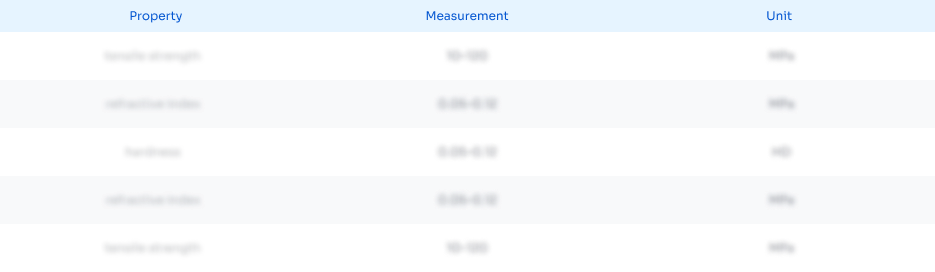
Abstract
Description
Claims
Application Information

- R&D
- Intellectual Property
- Life Sciences
- Materials
- Tech Scout
- Unparalleled Data Quality
- Higher Quality Content
- 60% Fewer Hallucinations
Browse by: Latest US Patents, China's latest patents, Technical Efficacy Thesaurus, Application Domain, Technology Topic, Popular Technical Reports.
© 2025 PatSnap. All rights reserved.Legal|Privacy policy|Modern Slavery Act Transparency Statement|Sitemap|About US| Contact US: help@patsnap.com