Processing technique for bamboo batten of bamboo floor
A processing technology, bamboo flooring technology, applied in wood processing equipment, manufacturing tools, wood treatment, etc., can solve problems such as wire skipping, cracking, and affecting floor quality, and achieve the effects of improving quality, avoiding wire skipping, and evenly distributing glue
- Summary
- Abstract
- Description
- Claims
- Application Information
AI Technical Summary
Problems solved by technology
Method used
Image
Examples
Embodiment 1
[0023] A processing technique for bamboo strips for a bamboo floor, comprising the following steps.
[0024] (1) The bamboo is cut off as required and then fragmented, and the bamboo joints are removed to obtain bamboo chips.
[0025] (2) The bamboo slices are further finely dissected, and the bamboo green bamboo slices are separated from the bamboo yellow bamboo slices.
[0026] (3) Pass the bamboo yellow bamboo slices through a bamboo strip press wheel crusher to press the bamboo yellow bamboo slices into fiber bamboo strands like bamboo strands.
[0027] (4) Carbonize or bleach the bamboo strips.
[0028] (5) Put the bamboo strips obtained in step (4) into a drying room and dry until the water content is 7%.
[0029] The bamboo strip roller crusher in step (3) comprises a base 1, a motor 2, a wire drawing machine 3, and also includes a strip cutter 4 and at least one set of roller presses 5, the motor 2, the wire drawing machine 3, the strip cutter 4 and the roller press...
Embodiment 2
[0031] A processing technique for bamboo strips for a bamboo floor, comprising the following steps.
[0032] (1) The bamboo is cut off as required and then fragmented, and the bamboo joints are removed to obtain bamboo chips.
[0033] (2) The bamboo slices are further finely dissected, and the bamboo green bamboo slices are separated from the bamboo yellow bamboo slices.
[0034] (3) Pass the bamboo yellow bamboo slices through a bamboo strip press wheel crusher to press the bamboo yellow bamboo slices into fiber bamboo strands like bamboo strands.
[0035] (4) Carbonize or bleach the bamboo strips.
[0036] (5) Put the bamboo strips obtained in step (4) into a drying room and dry until the water content is 6%.
[0037] The bamboo strip roller crusher in step (3) comprises a base 1, a motor 2, a wire drawing machine 3, and also includes a strip cutter 4 and at least one set of roller presses 5, the motor 2, the wire drawing machine 3, the strip cutter 4 and the roller press...
Embodiment 3
[0039] A processing technique for bamboo strips for a bamboo floor, comprising the following steps.
[0040] (1) The bamboo is cut off as required and then fragmented, and the bamboo joints are removed to obtain bamboo chips.
[0041] (2) The bamboo slices are further finely dissected, and the bamboo green bamboo slices are separated from the bamboo yellow bamboo slices.
[0042] (3) Pass the bamboo yellow bamboo slices through a bamboo strip press wheel crusher to press the bamboo yellow bamboo slices into fiber bamboo strands like bamboo strands.
[0043] (4) Carbonize or bleach the bamboo strips.
[0044] (5) Put the bamboo strips obtained in step (4) into a drying room and dry until the water content is 5%.
[0045] The bamboo strip roller crusher in step (3) comprises a base 1, a motor 2, a wire drawing machine 3, and also includes a strip cutter 4 and at least one set of roller presses 5, the motor 2, the wire drawing machine 3, the strip cutter 4 and the roller press...
PUM
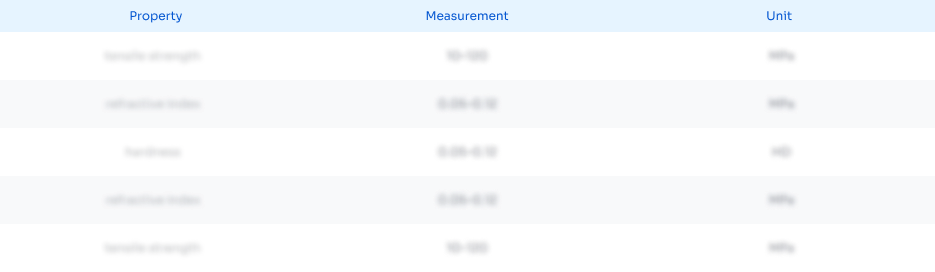
Abstract
Description
Claims
Application Information

- R&D
- Intellectual Property
- Life Sciences
- Materials
- Tech Scout
- Unparalleled Data Quality
- Higher Quality Content
- 60% Fewer Hallucinations
Browse by: Latest US Patents, China's latest patents, Technical Efficacy Thesaurus, Application Domain, Technology Topic, Popular Technical Reports.
© 2025 PatSnap. All rights reserved.Legal|Privacy policy|Modern Slavery Act Transparency Statement|Sitemap|About US| Contact US: help@patsnap.com