Integral high-frequency brazing process using welding fixtures
A welding fixture and process technology, applied in the direction of welding medium, welding equipment, welding/cutting medium/material, etc., can solve the problems of inconsistent clamping force, unstable welding quality, low efficiency of brazing and welding of a single gear block, etc., to achieve Stable welding quality, simple structure and long service life
- Summary
- Abstract
- Description
- Claims
- Application Information
AI Technical Summary
Problems solved by technology
Method used
Image
Examples
Embodiment 1
[0023] see Figure 1-2 It is a component schematic diagram and a component assembly schematic diagram of a welding fixture according to an embodiment of the present invention. Depend on Figure 1-2 It can be seen that the welding fixture of the present embodiment comprises a disc-shaped upper pressing plate (1) and a disc-shaped lower pressing plate (2), and the upper pressing plate (1) and the lower pressing plate (2) all have central positioning holes arranged coaxially (3), the lower pressing plate (2) is provided with a tooth block positioning hole (21), and the lower surface of the lower pressing plate (2) is provided with a tooth block installation groove (22), which is characterized in that the upper pressing plate (1) and the lower pressing plate (2) Install tooth block positioning screw (5) and tooth block compression spring (6); said lower pressing plate is also provided with 3 auxiliary positioning holes (4) evenly along the concentric ring; wherein the upper press...
Embodiment 2
[0025] In the process of this embodiment, the uniformly stirred silver-based solder and welding aid are evenly applied on the surface of the diamond tooth block to be brazed, and then the grinding disc substrate and the diamond tooth block are carried out using the welding fixture disclosed in Example 1. Position and fix, and then put it into a vacuum brazing furnace for brazing; the proportion of silver-based solder is Ag: 35wt%, Cu: 25wt%, Zn: 18wt%, Ni: 12wt%, Cd: 2wt %, Mn: 8wt%; the ratio of welding flux is: ZnCl 2 : 35wt%, NH 4 Cl: 35wt%, BaCl 2 : 10wt%, CaF 2 : 10wt%, borax: 10wt%; The addition ratio of silver-based solder and welding aid is 3: 1-5: 1; The average particle diameter of silver-based solder powder is 10-200um; The process parameter of brazing is: The brazing temperature is 690-715°C, the brazing time is 13-16s, and the vacuum degree is 0.01Pa.
PUM
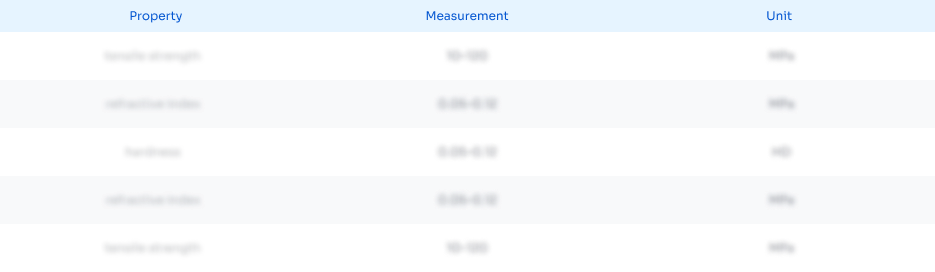
Abstract
Description
Claims
Application Information

- R&D
- Intellectual Property
- Life Sciences
- Materials
- Tech Scout
- Unparalleled Data Quality
- Higher Quality Content
- 60% Fewer Hallucinations
Browse by: Latest US Patents, China's latest patents, Technical Efficacy Thesaurus, Application Domain, Technology Topic, Popular Technical Reports.
© 2025 PatSnap. All rights reserved.Legal|Privacy policy|Modern Slavery Act Transparency Statement|Sitemap|About US| Contact US: help@patsnap.com