Energy-saving hydraulic shield propulsion system
A technology for shield tunneling and propulsion systems, which is applied in tunnels, mechanical equipment, fluid pressure actuation devices, etc., can solve the problems of high energy consumption, low overall hydraulic system efficiency, and large installed power.
- Summary
- Abstract
- Description
- Claims
- Application Information
AI Technical Summary
Problems solved by technology
Method used
Image
Examples
Embodiment Construction
[0015] Such as figure 1 As shown, the present invention includes a controller 5, a frequency converter 1, a frequency conversion motor 2, a quantitative pump 3, an oil tank 26, a first one-way valve 4, a two-position two-way electromagnetic reversing valve 6, a proportional overflow valve 7, and a speed regulating valve. Valve 8, three-position four-way electromagnetic directional valve 9, differential pressure reducing valve 10, first two-position three-way electromagnetic directional valve 11, second two-position three-way electromagnetic directional valve 12, proportional pressure reducing valve 13, The third one-way valve 24, the ball valve 25, the cartridge valve 20, the third two-position three-way electromagnetic reversing valve 21, the shuttle valve 19, the safety valve 18, the hydraulic control one-way valve 17, the second one-way valve 22, the third A hydraulic cylinder 16 , a second hydraulic cylinder 23 , a pressure sensor 15 and a built-in displacement sensor 14 i...
PUM
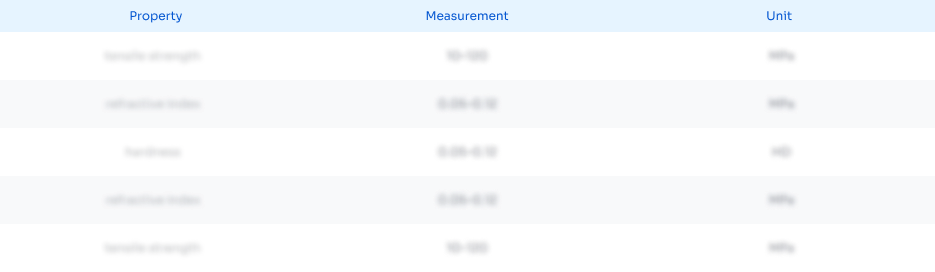
Abstract
Description
Claims
Application Information

- R&D Engineer
- R&D Manager
- IP Professional
- Industry Leading Data Capabilities
- Powerful AI technology
- Patent DNA Extraction
Browse by: Latest US Patents, China's latest patents, Technical Efficacy Thesaurus, Application Domain, Technology Topic, Popular Technical Reports.
© 2024 PatSnap. All rights reserved.Legal|Privacy policy|Modern Slavery Act Transparency Statement|Sitemap|About US| Contact US: help@patsnap.com