Dephosphorizing process of electric furnace steel making
A technology of electric furnace steelmaking and furnace charge, which is applied in the field of iron and steel metallurgy, can solve the problems of extended electric furnace smelting time, large consumption of electric energy and lime, and reduced production efficiency, and achieve the effects of shortening the smelting cycle, reducing costs, and broad application prospects
- Summary
- Abstract
- Description
- Claims
- Application Information
AI Technical Summary
Problems solved by technology
Method used
Examples
Embodiment 1
[0030] Embodiment 1 adopts the inventive method to produce dephosphorized molten steel
[0031] 70 tons of high-impedance ultra-high-power electric arc furnaces adopt the inventive method to produce 30CrMo (steel for high-pressure gas cylinder tubes), its process steps:
[0032] a. Steel and slag left at the eccentric bottom (steel and slag left at the eccentric bottom means that the tapping hole is not at the center of the furnace bottom, but deviates from the center of the furnace bottom for a certain distance, which is convenient for slag-free tapping). After tapping, scrap steel is added to the electric furnace 61.34t (including 6.81t of pig iron), mixed with 1500Kg of lime to make slag, mixed with 23.4t of molten iron.
[0033] b. For power supply, three oxygen burners are used to accelerate the melting of the metal charge. The power of each burner is 3.5MW. The metal charge is melted by 50-60%, and then 2000Kg of lime is added to form slag.
[0034] c. When the molten s...
Embodiment 2
[0038] Embodiment 2 adopts the inventive method to produce dephosphorized molten steel
[0039] The 70-ton high-impedance ultra-high-power electric arc furnace adopts the art of production of WB36CN1 (steel for nuclear power pipes), and its process steps:
[0040] a. Steel and slag left at the eccentric bottom (steel and slag left at the eccentric bottom means that the tapping hole is not at the center of the furnace bottom, but deviates from the center of the furnace bottom for a certain distance, which is convenient for slag-free tapping). After tapping, scrap steel is added to the electric furnace 62.64t (including 5t of pig iron), mixed with 1800Kg of lime to make slag, mixed with 21t of molten iron.
[0041] b. For power supply, three oxygen burners are used to accelerate the melting of the metal charge. The power of each burner is 3.5MW. The metal charge is melted by 50-60%, and then 2000Kg of lime is added to form slag.
[0042] c. When the temperature of the molten po...
Embodiment 3
[0046] Embodiment 3 adopts the inventive method to produce dephosphorized molten steel
[0047] The 70-ton high-impedance ultra-high-power electric arc furnace adopts the art of production of 27CrMo (steel for oil pipes), and its process steps:
PUM
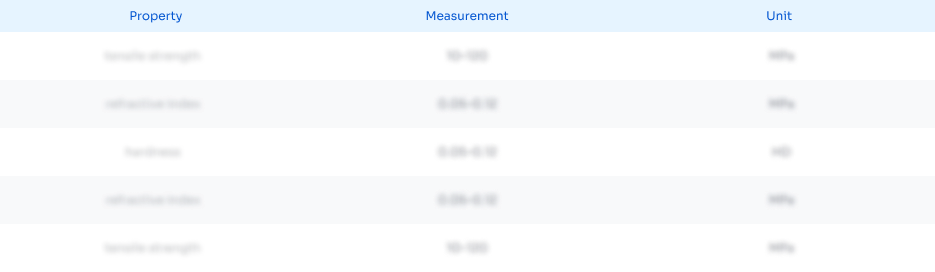
Abstract
Description
Claims
Application Information

- Generate Ideas
- Intellectual Property
- Life Sciences
- Materials
- Tech Scout
- Unparalleled Data Quality
- Higher Quality Content
- 60% Fewer Hallucinations
Browse by: Latest US Patents, China's latest patents, Technical Efficacy Thesaurus, Application Domain, Technology Topic, Popular Technical Reports.
© 2025 PatSnap. All rights reserved.Legal|Privacy policy|Modern Slavery Act Transparency Statement|Sitemap|About US| Contact US: help@patsnap.com