Catalyst containing nickel-iron-manganese compound oxide for processing industrial waste gas and preparation method thereof
A composite oxide and industrial waste gas technology, which is applied in physical/chemical process catalysts, metal/metal oxide/metal hydroxide catalysts, molecular sieve catalysts, etc., can solve the problems of poor practical performance, poor anti-toxicity, and high price and other problems, to achieve the effect of easy expansion and reproduction, low cost and convenient operation
- Summary
- Abstract
- Description
- Claims
- Application Information
AI Technical Summary
Problems solved by technology
Method used
Image
Examples
Embodiment 1
[0036] (1) Preparation of self-made cordierite carrier
[0037] Take 30g of silica, 40g of alumina and 30g of magnesia and mix evenly. The mixture is roasted at 1300°C, and the holding time is controlled at 6h; the self-made carrier is modified with oxalic acid solution with a mass concentration of 5%, boiled on an electric furnace and kept for 2h. The drying temperature was 80°C, and the drying time was 2 h; the calcination temperature was 400°C, and the calcination time was 6 h, and the self-made cordierite carrier was obtained;
[0038] (2) Modification of self-made cordierite carrier
[0039] Take the above-mentioned 50g carrier and impregnate it in alumina sol for 4 hours, dry it at 80°C for 2 hours, and then roast it at 500°C for 4 hours to obtain a modified cordierite carrier with a mass percentage of alumina of 1%;
[0040] (3) Preparation of nickel-iron-manganese composite oxide catalyst
[0041] Take 50 g of the self-made carrier sample in step (2) and impregna...
Embodiment 2
[0046] (1) Preparation of self-made cordierite carrier
[0047] Take 35g of silica, 40g of alumina and 25g of magnesia and mix evenly. The mixture is roasted at 1400°C, and the holding time is controlled at 6h; the self-made carrier is modified by nitric acid solution with a mass concentration of 10%, boiled on an electric furnace and kept for 2h. The drying temperature was 80°C, and the drying time was 2 h; the calcination temperature was 400°C, and the calcination time was 6 h, and the self-made cordierite carrier was obtained;
[0048] (2) Modification of self-made cordierite carrier
[0049] Take the above-mentioned 50g carrier and impregnate it in silica sol for 4 hours, dry it at 80°C for 2 hours, and then roast it at 500°C for 4 hours to obtain a modified cordierite carrier with a mass percentage of silicon oxide of 4%;
[0050] (3) Preparation of nickel-iron-manganese composite oxide catalyst
[0051] Take 50 g of the self-made carrier sample in step (2) and impr...
Embodiment 3
[0056] (1) Preparation of self-made cordierite carrier
[0057] Take 55g of silicon oxide, 20g of aluminum oxide and 25g of magnesium oxide and mix evenly. The mixture is roasted at 1400°C, and the holding time is controlled at 4h; the self-made carrier is modified with acetic acid solution with a mass concentration of 20%, boiled on an electric furnace and kept for 3h. The drying temperature was 120°C, and the drying time was 1 h; the calcination temperature was 600°C, and the calcination time was 4 h, and the self-made cordierite carrier was obtained;
[0058] (2) Modification of self-made cordierite carrier
[0059] Take the above-mentioned 50g carrier and impregnate it in silica sol for 6 hours, dry it at 120°C for 1 hour, and then roast it at 600°C for 2 hours to obtain a modified cordierite carrier with a mass percentage of silicon oxide of 10%;
[0060] (3) Preparation of nickel-iron-manganese composite oxide catalyst
[0061] Take 50 g of the self-made carrier sa...
PUM
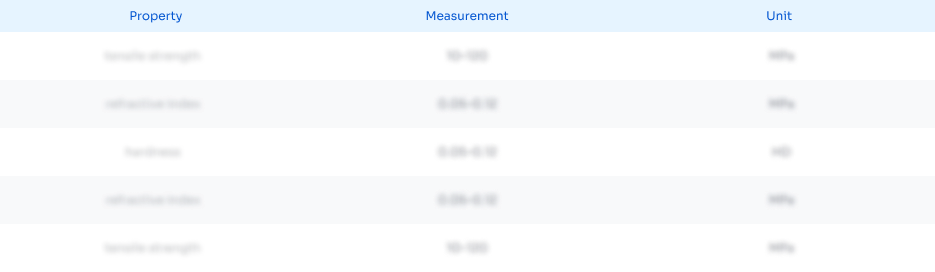
Abstract
Description
Claims
Application Information

- R&D Engineer
- R&D Manager
- IP Professional
- Industry Leading Data Capabilities
- Powerful AI technology
- Patent DNA Extraction
Browse by: Latest US Patents, China's latest patents, Technical Efficacy Thesaurus, Application Domain, Technology Topic, Popular Technical Reports.
© 2024 PatSnap. All rights reserved.Legal|Privacy policy|Modern Slavery Act Transparency Statement|Sitemap|About US| Contact US: help@patsnap.com