Electric conduction composite material with poly-2, 3-dimethylaniline/polyaniline core shell structure and preparation method of electric conduction composite material
A conductive composite material, dimethyl aniline technology, applied in the field of composite materials, can solve the problems of low conductivity, difficulty in making conductive, limiting sensor research, etc., and achieve the effect of improving conductivity
- Summary
- Abstract
- Description
- Claims
- Application Information
AI Technical Summary
Problems solved by technology
Method used
Image
Examples
experiment example 1
[0024] Add 25ml distilled water 8.2×10 to reactor A successively -3 mol concentrated hydrochloric acid (commercially available content 36~38%) and 8.15×10 -3 mol 2,3-dimethylaniline, stirred for 30 minutes to make it evenly mixed; dripped 12.5ml of 1.2mol / L ammonium persulfate solution, stirred and reacted at 30°C for 12 hours; filtered with suction, washed the filter cake with distilled water until the filtrate was colorless; The filter cake was dried at 60° C. for 12 hours, taken out and ground into powder to obtain powdered poly-2,3-dimethylaniline. Move the powder into reactor B, add 150ml 1.2mol / L hydrochloric acid solution, stir to disperse evenly; add 3.29×10 -2 mol aniline (3ml), stir for 30min; slowly drop 22.7ml 0.58mol / L ammonium persulfate solution into the system, stir and react at 30°C for 5h; filter with suction, wash the filter cake with 0.1mol / L hydrochloric acid solution until the filtrate is colorless . The filter cake was dried at 60°C for 12 hours, take...
experiment example 2
[0026] Add 25ml distilled water 8.2×10 to reactor A successively -3 mol concentrated hydrochloric acid (commercially available content 36~38%) and 8.15×10 -3 mol 2,3-dimethylaniline, stirred for 30 minutes to make it evenly mixed; dropwise added 12.5ml 1.2mol / L sodium persulfate solution, stirred and reacted at 30°C for 12 hours; filtered with suction, washed the filter cake with distilled water until the filtrate was colorless; The filter cake was dried at 60° C. for 12 hours, taken out and ground into powder to obtain powdered poly-2,3-dimethylaniline. Move the powder into reactor B, add 37.5ml of 1.2mol / L hydrochloric acid solution, stir to disperse evenly; add 8.15×10 -3 mol aniline (0.75ml), stirred for 30min; slowly dripped 14.1ml 0.58mol / L sodium persulfate solution into the system, stirred and reacted at 0°C for 8h; suction filtered, washed the filter cake with 0.1mol / L hydrochloric acid solution until the filtrate was free color. The filter cake was dried at 60°C f...
experiment example 3
[0028] Add 25ml distilled water 8.2×10 to reactor A successively -3 mol concentrated hydrochloric acid (commercially available content 36~38%) and 8.15×10 -3 mol 2,3-dimethylaniline, stirred for 30 minutes to make it evenly mixed; 12.5ml of 1.2mol / L sodium persulfate solution was added dropwise, stirred and reacted at 30°C for 12 hours, filtered with suction, and the filter cake was washed with distilled water until the filtrate was colorless; The filter cake was dried at 60° C. for 12 hours, taken out and ground into powder to obtain powdered poly-2,3-dimethylaniline. Move the powder into reactor B, add 150ml of 1.2mol / L hydrochloric acid solution, stir to disperse evenly; then add 1.97×10 -2 mol sodium dodecylbenzenesulfonate and 3.29×10 -2 mol aniline (3ml), emulsify for 30min; slowly drop 22.7ml 0.58mol / L sodium persulfate solution into the system, stir and react at 30°C for 8h; after the reaction, add 30ml saturated NaCl solution to reactor B to break the emulsion 30mi...
PUM
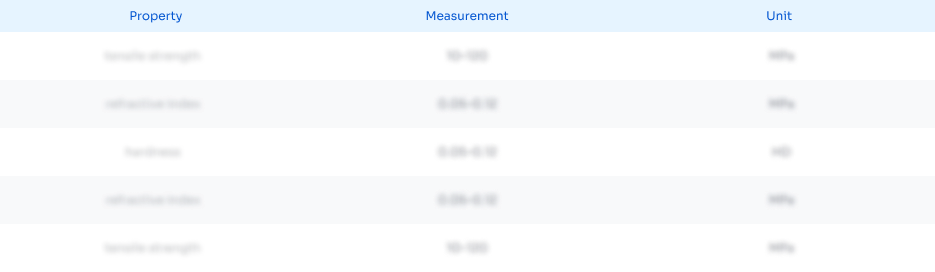
Abstract
Description
Claims
Application Information

- R&D
- Intellectual Property
- Life Sciences
- Materials
- Tech Scout
- Unparalleled Data Quality
- Higher Quality Content
- 60% Fewer Hallucinations
Browse by: Latest US Patents, China's latest patents, Technical Efficacy Thesaurus, Application Domain, Technology Topic, Popular Technical Reports.
© 2025 PatSnap. All rights reserved.Legal|Privacy policy|Modern Slavery Act Transparency Statement|Sitemap|About US| Contact US: help@patsnap.com