Ingot mould used for casting iron alloy and casting method thereof
A cast iron alloy and ferroalloy technology, which is applied in the field of ferroalloy casting ingot mold, cast iron alloy ingot mold and casting field, can solve the problems of low economic benefit, high energy consumption, burning loss of ore raw material resources, etc., and achieve significant economic benefits, The effect of reducing labor intensity and improving production environment
- Summary
- Abstract
- Description
- Claims
- Application Information
AI Technical Summary
Problems solved by technology
Method used
Image
Examples
Embodiment Construction
[0039] A kind of ingot mold that the present invention proposes is used for cast iron alloy, and it is made of mold body 1 and configuration
[0040] The demoulding iron 9 in the casting cavity 2 of the mold body 1 is formed, and the mold wall 10 around the mold body 1 is made into an outwardly inclined demoulding structure, for example: the length of the casting cavity 2 is 1800mm, the width is 1000mm, and the depth For an ingot mold with a rectangular structure of 180mm, the camber angle α of the mold wall 10 is set to 30o. This cambered demoulding structure design is particularly beneficial to the operation of removing iron from the mold; another example: the length of the casting cavity 2 is 3500mm For an ingot mold with a rectangular structure with a width of 2500 mm and a depth of 120 mm, the camber angle α of the mold wall 10 is set to 60o for a cambered demoulding structure, which is also conducive to the operation of removing iron from the mold. According to the speci...
PUM
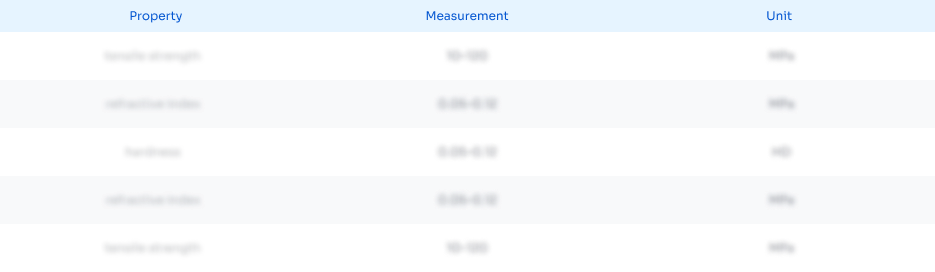
Abstract
Description
Claims
Application Information

- R&D
- Intellectual Property
- Life Sciences
- Materials
- Tech Scout
- Unparalleled Data Quality
- Higher Quality Content
- 60% Fewer Hallucinations
Browse by: Latest US Patents, China's latest patents, Technical Efficacy Thesaurus, Application Domain, Technology Topic, Popular Technical Reports.
© 2025 PatSnap. All rights reserved.Legal|Privacy policy|Modern Slavery Act Transparency Statement|Sitemap|About US| Contact US: help@patsnap.com