Capacitive touch screen and manufacture method thereof
A technology of capacitive touch screen and printed circuit layer, which is applied to the input/output process of electrical digital data processing, instruments, and data processing, etc. The effect of less image distortion and stable dielectric constant
- Summary
- Abstract
- Description
- Claims
- Application Information
AI Technical Summary
Problems solved by technology
Method used
Image
Examples
Embodiment Construction
[0023] Please refer to figure 1 , The present invention provides a capacitive touch screen, including an ITO glass substrate 1 , a printed circuit layer 2 and a PET film 3 .
[0024] Wherein, both the front and the back of the ITO glass substrate 1 are provided with a printed circuit layer 2 , and the printed circuit layer 2 is bonded to a flexible circuit board (FPC) 20 . Usually, the printed circuit layer 2 is printed and formed on the surface of the ITO glass substrate 1 first, and then the flexible circuit board 20 is bonded to the ITO glass substrate 1 to electrically connect with the printed circuit layer on the corresponding side.
[0025] The PET film 3 is pasted on the outer surface of the corresponding printed circuit layer 2 on the ITO glass substrate 1 through the adhesive layer 30 . According to the needs of product design, PET film 3 can only be pasted on the outer surface of the printed circuit layer 2 on the front of the ITO glass, or PET film 3 can be pasted ...
PUM
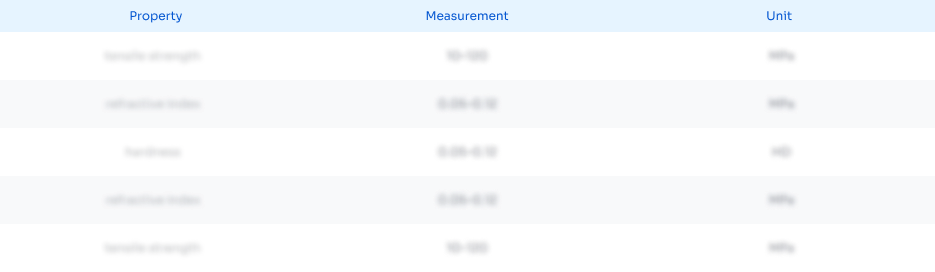
Abstract
Description
Claims
Application Information

- R&D
- Intellectual Property
- Life Sciences
- Materials
- Tech Scout
- Unparalleled Data Quality
- Higher Quality Content
- 60% Fewer Hallucinations
Browse by: Latest US Patents, China's latest patents, Technical Efficacy Thesaurus, Application Domain, Technology Topic, Popular Technical Reports.
© 2025 PatSnap. All rights reserved.Legal|Privacy policy|Modern Slavery Act Transparency Statement|Sitemap|About US| Contact US: help@patsnap.com