Processing method for acid gas containing H2S
A treatment method and acid gas technology, applied in separation methods, chemical instruments and methods, inorganic chemistry, etc., can solve problems such as complex control and operation, large circulating liquid in the absorption tower, and slow reaction speed, so as to reduce operation difficulty and cost , the effect of reduced washing cycle volume, reduced height and diameter
- Summary
- Abstract
- Description
- Claims
- Application Information
AI Technical Summary
Problems solved by technology
Method used
Image
Examples
Embodiment 1
[0033] figure 1 It is a simplified flowchart of the treatment method for acid gas combustion and purification in the present invention. Such as figure 1 Shown, air 1 (can also use oxygen or other fuel gas), is divided into two parts, one part enters SO 2 Go to SO 3 Reactor 6, the other part is mixed with acid gas 2 according to a certain ratio and enters combustion chamber 3, the volume of the acid gas entering combustion chamber (also can adopt reactor) 3 is 45% of total volume, acid gas and air ratio are about 1.5: 1 (volume ratio). The reaction temperature of thermal incineration in the combustion chamber is 900°C.
[0034] The gas after incineration enters the first waste heat boiler 4, and its temperature is reduced to suitable for SO 2 Go to SO 3 The temperature required for the reaction is about 420°C, and the first steam 5 with low pressure is generated and discharged.
[0035] The incinerated and cooled gas then enters the SO 2 Go to SO 3 Reactor 6, where SO ...
Embodiment 2
[0051] The acid gas treatment process is basically the same as in Example 1, the difference is that it is converted into SO 2 During the reaction, oxygen is used as fuel for catalytic incineration, and the catalyst loading is about 0.8m 3 , the reaction temperature is 500°C. The volume of the acid gas entering the combustion chamber 3 is 20% of the total volume, and the ratio of the amount of oxygen introduced to the volume of the acid gas entering the combustion chamber 3 is 0.5:1.
[0052] SO 2 Go to SO 3 During the reaction, the reaction temperature is 550°C, and the contained SO 2 Gas and O 2 The molar ratio of the amount used is 1:4, the catalyst is a platinum catalyst, and the amount is 5m 2 platinum net.
[0053] SO 3 React with ammonia water 9 to generate sulfate, the temperature is 55°C, the concentration of ammonia water is 3%, containing SO 3 The molar ratio of gas to ammonia water 9 is 1:1.4.
[0054] The composition of raw acid gas 2 in the present embodi...
Embodiment 3
[0065] The acid gas treatment process is basically the same as in Example 1, the difference is that it is converted into SO 2 During the reaction, the combustion reaction temperature is 550°C. The volume of the acid gas entering the combustion chamber 3 is about 20% of the total volume, and the molar ratio of the acid gas to the amount of air introduced is 1.8:1.
[0066] SO 2 Go to SO 3 During the reaction, the reaction temperature is 350°C, and the contained SO 2 Gas and O 2 The dosage ratio is 1:6, the catalyst is platinum catalyst, and the dosage is 7m 2 .
[0067] SO 3 React with ammonia water 9 to generate sulfate, the temperature is 45°C, the concentration of ammonia water is 15%, containing SO 3 The ratio of gas to ammonia 9 is 1:4.
[0068] The composition of raw acid gas 2 in the present embodiment is as follows:
[0069] composition
[0070] O 2
[0071] go to SO 2 Go to SO 3 The composition and content of reactor 6 are as follows: ...
PUM
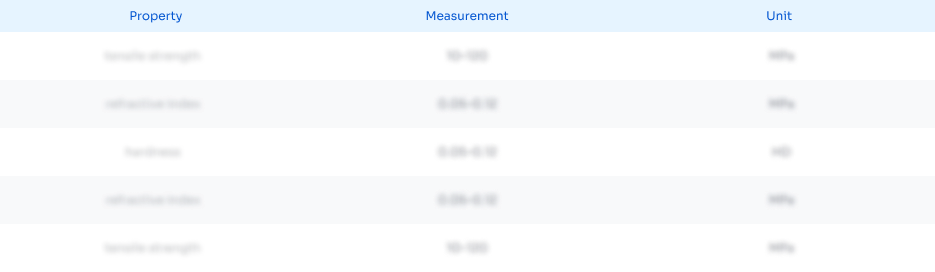
Abstract
Description
Claims
Application Information

- R&D
- Intellectual Property
- Life Sciences
- Materials
- Tech Scout
- Unparalleled Data Quality
- Higher Quality Content
- 60% Fewer Hallucinations
Browse by: Latest US Patents, China's latest patents, Technical Efficacy Thesaurus, Application Domain, Technology Topic, Popular Technical Reports.
© 2025 PatSnap. All rights reserved.Legal|Privacy policy|Modern Slavery Act Transparency Statement|Sitemap|About US| Contact US: help@patsnap.com