Superhigh-efficiency brazed motor rotor
An electric motor, ultra-efficient technology, applied in the direction of magnetic circuit rotating parts, magnetic circuit shape/style/structure, etc., can solve the problems of difficulty in die-casting process, increase of stray loss of transverse harmonic current, increase of motor cost, etc., to achieve The effect of simple equipment tooling, reducing stray loss, and reducing temperature rise
- Summary
- Abstract
- Description
- Claims
- Application Information
AI Technical Summary
Problems solved by technology
Method used
Image
Examples
Embodiment
[0045] This embodiment design rated voltage 380V, rated frequency 50Hz, Wiring, sealed self-fan cooling, protection class IP55, insulation class F, N design for general use. According to the national standard GB18613-2006 "small and medium-sized three-phase asynchronous motor energy efficiency limit value and energy efficiency level" the highest level and related standards assessment. The motor efficiency is determined according to the loss analysis method B in GB / T1032-2005 "Test methods for three-phase asynchronous motors".
[0046] See Table 1 and Table 2 for motor structural parameters and performance target targets (including energy efficiency limit values including rated output power and 75% rated output power efficiency). The model, rated power and number of poles of the embodiment are as follows:
example 1
[0047] Example 1: CGX132S1-2, 5.5kW, 2 poles;
example 2
[0048] Example 2: CGX132S-4, 5.5kW, 4 poles;
PUM
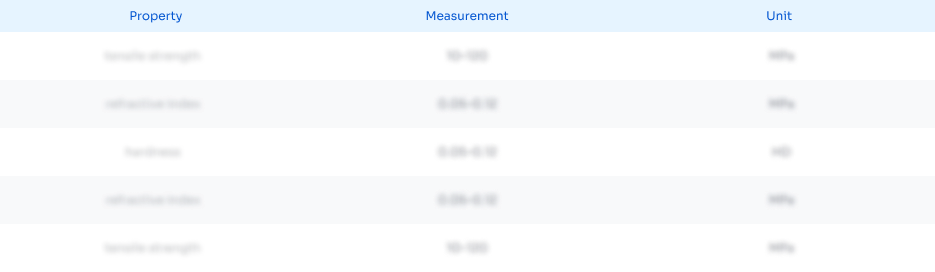
Abstract
Description
Claims
Application Information

- R&D
- Intellectual Property
- Life Sciences
- Materials
- Tech Scout
- Unparalleled Data Quality
- Higher Quality Content
- 60% Fewer Hallucinations
Browse by: Latest US Patents, China's latest patents, Technical Efficacy Thesaurus, Application Domain, Technology Topic, Popular Technical Reports.
© 2025 PatSnap. All rights reserved.Legal|Privacy policy|Modern Slavery Act Transparency Statement|Sitemap|About US| Contact US: help@patsnap.com