Technology for processing comprehensive waste water from acrylonitrile and acrylic fibers production
A technology that integrates waste water and treatment processes, applied in the field of environmental engineering, can solve the problems of difficult actual operation, easy pollution of membrane systems, high investment and operation costs, etc., and achieve the effect of improving biological treatment performance and high removal rate of total sulfur
- Summary
- Abstract
- Description
- Claims
- Application Information
AI Technical Summary
Problems solved by technology
Method used
Image
Examples
Embodiment 1
[0037]The comprehensive wastewater from the production of acrylonitrile and acrylic fiber in Nanjing, Jiangsu Province is firstly filtered through the grid and then placed in the regulating pool for standby. After testing, the pH of the pond effluent was adjusted to 7.2, in which COD was 6,100 mg / L and total nitrogen was 450 mg / L.
[0038] The comprehensive wastewater from the production of acrylonitrile and acrylic fiber first enters the pre-aeration reaction tank, reacts with the reflux acidification liquid and reflux sludge, and then enters the hydrolysis acidification reaction tank. The aeration intensity (DO value) is 0.5 mg / L.
[0039] The wastewater after pre-aeration treatment enters the hydrolytic acidification tank for hydrolytic acidification treatment. Phosphorus-containing nutrients (sodium dihydrogen phosphate) are added to the hydrolytic acidification tank, and the waste water is reduced under the action of sulfate-reducing bacteria naturally existing in the slud...
Embodiment 2
[0046] The comprehensive waste water from the production of acrylonitrile and acrylic fiber in Wuxi, Jiangsu Province was first filtered through the grid and then placed in the regulating pool for standby. After testing, the pH of the pond effluent was adjusted to 6.8, with COD 5,890mg / L and total nitrogen 553mg / L.
[0047] The comprehensive wastewater from acrylonitrile and acrylic fiber production first enters the pre-aeration reaction tank, reacts with reflux acidification liquid and reflux sludge, and then enters the hydrolysis acidification reaction tank. The aeration intensity (DO value) is 1.0 mg / L.
[0048] The wastewater after pre-aeration treatment enters the hydrolytic acidification tank for hydrolytic acidification treatment. Phosphorus-containing nutrients (disodium hydrogen phosphate) are added to the hydrolytic acidification tank, and the wastewater SO 4 2- converted to H 2 S, part of the acidification solution is returned to the pre-aeration reaction tank, a...
Embodiment 3
[0055] The comprehensive wastewater from the production of acrylonitrile and acrylic fiber in Nanjing, Jiangsu Province is firstly filtered through the grid and then placed in the regulating pool for standby. After testing, the pH of the pond effluent was adjusted to 7.8, with COD 4,500mg / L and total nitrogen 380mg / L.
[0056] The comprehensive wastewater from acrylonitrile and acrylic fiber production first enters the pre-aeration reaction tank, reacts with the reflux acidification liquid and the reflux sludge, and then enters the hydrolysis acidification reaction tank. The aeration intensity (DO value) is 0.8 mg / L.
[0057] The wastewater after pre-aeration treatment enters the hydrolytic acidification tank for hydrolytic acidification treatment. Phosphorus-containing nutrients (dipotassium hydrogen phosphate) are added to the hydrolytic acidification tank, and the waste water SO 4 2- converted to H 2 S, part of the acidification solution is returned to the pre-aeration r...
PUM
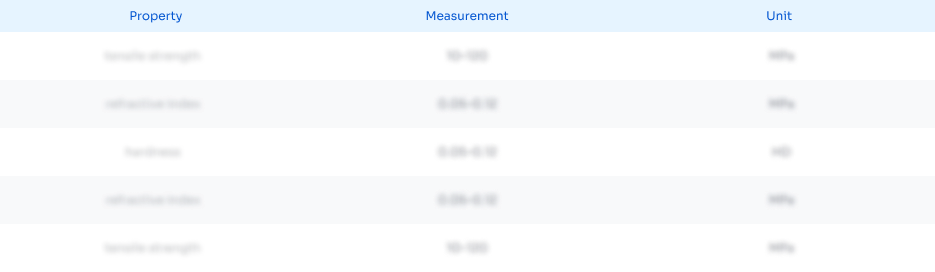
Abstract
Description
Claims
Application Information

- R&D
- Intellectual Property
- Life Sciences
- Materials
- Tech Scout
- Unparalleled Data Quality
- Higher Quality Content
- 60% Fewer Hallucinations
Browse by: Latest US Patents, China's latest patents, Technical Efficacy Thesaurus, Application Domain, Technology Topic, Popular Technical Reports.
© 2025 PatSnap. All rights reserved.Legal|Privacy policy|Modern Slavery Act Transparency Statement|Sitemap|About US| Contact US: help@patsnap.com