Multi-phase crystallization method
A crystallization and crystallizer technology, applied in the direction of solution crystallization, can solve the problems of low production capacity and crystallizer scarring, and achieve the effect of improving production capacity and good technical effect.
- Summary
- Abstract
- Description
- Claims
- Application Information
AI Technical Summary
Problems solved by technology
Method used
Image
Examples
Embodiment 1
[0020] Method for separating p-xylene from mixed xylene of the present invention
[0021] Such as figure 2 Said, the mixed xylene raw material 2 from the raw material tank 1 and the diluent 14 from the diluent storage tank 13 are crystallized in the crystallizer 3, wherein the concentration of p-xylene in the mixed xylene raw material is 81% (mass), The concentration of m-xylene is 19% (mass), the mass ratio of the diluent 14 to the mixed xylene raw material 2 is 0.2:1, the diluent is ammonia water, the crystallizer crystallization temperature is -15℃, the crystal slurry 4 is solid-liquid After separation by separator 5, crystals 6 and a mixture of diluent and crystallization mother liquor 8 are obtained; crystals 6 are washed by diluent 15 and enter product tank 7, and the detergent is ammonia; the mixture 8 of diluent and crystallization mother liquor is separated by separator 9 The crystallization mother liquor 10 and the diluent 12 enter the mother liquor tank 11, and the d...
Embodiment 2
[0023] Method for separating p-xylene from mixed xylene of the present invention
[0024] Such as figure 2 Said, the mixed xylene raw material 2 from the raw material tank 1 and the diluent 14 from the diluent storage tank 13 are crystallized in the crystallizer 3, wherein the concentration of p-xylene in the mixed xylene raw material is 81% (mass), The concentration of m-xylene is 19% (mass), the mass ratio of the diluent 14 to the mixed xylene raw material 2 is 0.5:1, the diluent is ammonia, the crystallizer crystallization temperature is -25°C, the crystal slurry 4 is solid-liquid After separation by separator 5, crystals 6 and a mixture of diluent and crystallization mother liquor 8 are obtained; crystals 6 are washed by diluent 15 and enter product tank 7, and the detergent is ammonia; the mixture 8 of diluent and crystallization mother liquor is separated by separator 9 The crystallization mother liquor 10 and the diluent 12 enter the mother liquor tank 11, and the diluen...
Embodiment 3
[0026] Method for separating p-xylene from mixed xylene of the present invention
[0027] Such as figure 2 Said, the mixed xylene raw material 2 from the raw material tank 1 and the diluent 14 from the diluent storage tank 13 are crystallized in the crystallizer 3, wherein the concentration of p-xylene in the mixed xylene raw material is 81% (mass), The concentration of m-xylene is 19% (mass), the mass ratio of the diluent 14 to the mixed xylene raw material 2 is 0.5:1, the diluent is methanol, the crystallizer crystallization temperature is -25℃, and the slurry 4 is solid-liquid After separation by separator 5, crystals 6 and a mixture of diluent and crystallization mother liquor 8 are obtained; crystals 6 are washed by diluent 15 and then enter product tank 7, and the detergent is methanol; the mixture 8 of diluent and crystallization mother liquor is separated by separator 9 The crystallization mother liquor 10 and the diluent 12 enter the mother liquor tank 11, and the dilu...
PUM
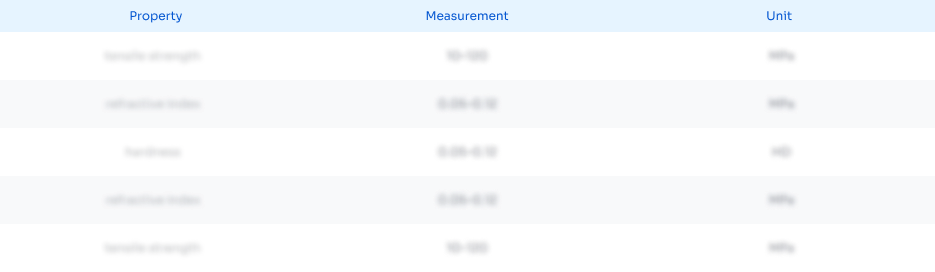
Abstract
Description
Claims
Application Information

- Generate Ideas
- Intellectual Property
- Life Sciences
- Materials
- Tech Scout
- Unparalleled Data Quality
- Higher Quality Content
- 60% Fewer Hallucinations
Browse by: Latest US Patents, China's latest patents, Technical Efficacy Thesaurus, Application Domain, Technology Topic, Popular Technical Reports.
© 2025 PatSnap. All rights reserved.Legal|Privacy policy|Modern Slavery Act Transparency Statement|Sitemap|About US| Contact US: help@patsnap.com