Injection die for injection and pull-extrusion process and method for preparing resin matrix composite by using same
A technology of injection mold and pultrusion process, which is applied in the field of injection mold and the preparation of resin-based composite materials by using it, which can solve the problems of cumbersome structure of injection mold, reduce the probability of worker's misoperation, expand the application range, and improve the mechanical properties.
- Summary
- Abstract
- Description
- Claims
- Application Information
AI Technical Summary
Problems solved by technology
Method used
Image
Examples
specific Embodiment approach 1
[0019] Specific implementation mode one: combined with figure 1 , indicating that the present embodiment is an injection mold for injection pultrusion process, the injection mold is provided with a mold cavity 1 and a glue injection hole 2, and the mold cavity 1 is composed of a frustum-shaped mold cavity 1-1 and a cylindrical mold cavity 1-2, The glue injection hole 2 is located on the mold wall of the truncated conical mold cavity 1-1, and the glue injection hole 2 is connected with the truncated conical mold cavity 1-1. The small-diameter end of the cavity 1-1 is connected with one end of the cylindrical cavity 1-2, and the diameter of the small-diameter port of the frustum-shaped cavity 1-1 is the same as that of the cylindrical cavity 1-2, and the cylindrical cavity 1 The other end of -2 is in sealing communication with the mold cavity of the pultrusion mold 3, and the outer wall of the injection mold is screwed with the pultrusion mold 3.
[0020] The mold cavity of the...
specific Embodiment approach 2
[0021] Embodiment 2: The difference between this embodiment and Embodiment 1 is that a circulating water cooling device 4 is provided on the outer wall of the pultrusion mold 3 where the outer wall of the injection mold is screwed to the pultrusion mold 3 . Other parameters and connection relations are the same as those in the first embodiment.
[0022] This embodiment is equipped with a circulating water cooling device, which can prevent the resin from solidifying in the injection dipping tooling due to heat transfer due to long-term use.
specific Embodiment approach 3
[0023] Embodiment 3: This embodiment differs from Embodiment 1 or Embodiment 2 in that the number of injection holes 2 is 1 to 4, which are evenly distributed on the mold wall of the truncated conical mold cavity 1-1. Other parameters and connection relations are the same as those in Embodiment 1 or Embodiment 2.
[0024] In this embodiment, the number and position of the injection holes can be adjusted according to the amount of yarn and the viscosity of the resin.
PUM
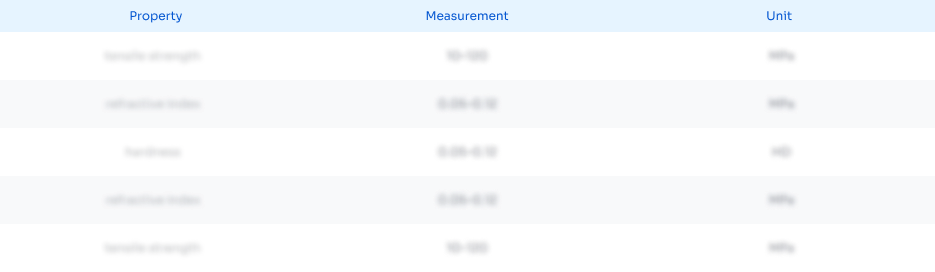
Abstract
Description
Claims
Application Information

- R&D
- Intellectual Property
- Life Sciences
- Materials
- Tech Scout
- Unparalleled Data Quality
- Higher Quality Content
- 60% Fewer Hallucinations
Browse by: Latest US Patents, China's latest patents, Technical Efficacy Thesaurus, Application Domain, Technology Topic, Popular Technical Reports.
© 2025 PatSnap. All rights reserved.Legal|Privacy policy|Modern Slavery Act Transparency Statement|Sitemap|About US| Contact US: help@patsnap.com