Slurry for desulfuration and denitration of recirculating fluidized bed boiler
A circulating fluidized bed, desulfurization and denitration technology, applied in chemical instruments and methods, separation methods, dispersed particle separation, etc., can solve the problems of low utilization rate of desulfurizers and low desulfurization efficiency, and achieve improved desulfurization performance, good effect, Realize the effect of comprehensive utilization
- Summary
- Abstract
- Description
- Claims
- Application Information
AI Technical Summary
Problems solved by technology
Method used
Image
Examples
Embodiment 1
[0021] A thermal power plant uses raw coal with a sulfur content of 1.94% and a nitrogen content of 0.89%.
[0022] Desulfurization agent ratio: limestone 78% (fineness 2 and NO x The reaction produces sulfate and N 2 .
[0023] In the same coal-fired boiler, the concentrations of sulfur dioxide and nitrogen oxides were measured before and after the desulfurization and denitrification agent slurry was injected.
[0024] Average emission concentration of sulfur dioxide before desulfurization and denitrification: 4212mg / m 3 , the average emission concentration of nitrogen oxides is 215mg / m 3 , after spraying the desulfurization and denitrification agent slurry, the average emission concentration of sulfur dioxide was measured to be 326mg / m 3 , the average emission concentration of nitrogen oxides is 69mg / m 3 , ammonia escape is less than 5mg / m 3 .
Embodiment 2
[0026] A company's self-owned power plant uses raw coal with a sulfur content of 0.73% and a nitrogen content of 0.71%.
[0027] Desulfurization agent ratio: limestone 78% (fineness 2 and NO x The reaction produces sulfate and N 2 .
[0028] In the same coal-fired boiler, the concentrations of sulfur dioxide and nitrogen oxides were measured before and after the desulfurization and denitrification agent slurry was injected.
[0029] Average emission concentration of sulfur dioxide before desulfurization and denitrification: 1538mg / m 3 , the average emission concentration of nitrogen oxides is 163mg / m 3 , after spraying the desulfurization and denitrification agent slurry, the average emission concentration of sulfur dioxide was measured to be 145mg / m 3 , the average emission concentration of nitrogen oxides is 54mg / m 3 , ammonia escape is less than 5mg / m 3 .
Embodiment 3
[0031] A company's self-owned power plant uses raw coal with a sulfur content of 1.43% and a nitrogen content of 0.82%.
[0032] Desulfurizer ratio: limestone 80% (fineness 2 and NO x The reaction produces sulfate and N 2 .
PUM
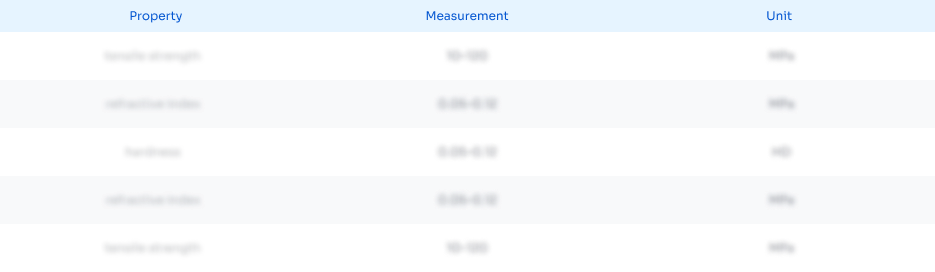
Abstract
Description
Claims
Application Information

- R&D
- Intellectual Property
- Life Sciences
- Materials
- Tech Scout
- Unparalleled Data Quality
- Higher Quality Content
- 60% Fewer Hallucinations
Browse by: Latest US Patents, China's latest patents, Technical Efficacy Thesaurus, Application Domain, Technology Topic, Popular Technical Reports.
© 2025 PatSnap. All rights reserved.Legal|Privacy policy|Modern Slavery Act Transparency Statement|Sitemap|About US| Contact US: help@patsnap.com