Method for preparing phenolic chemicals through thermo-chemical conversion of industrial lignin
An industrial lignin and thermochemical conversion technology, which is applied in the field of industrial lignin thermochemical conversion to prepare phenolic chemicals, can solve the problems of high equipment requirements, constant, high energy consumption, etc., and achieve simple recovery process and wide sources , the effect of reducing production costs
- Summary
- Abstract
- Description
- Claims
- Application Information
AI Technical Summary
Problems solved by technology
Method used
Image
Examples
Embodiment 1
[0042] A component:
[0043] Acid-precipitated lignin from papermaking black liquor 100g
[0044] Aluminosilicate 5 g
[0045]Tetrahydronaphthalene 7 g
[0046] B component:
[0047] Glycerin 300 g
[0048] Dry the acid-precipitated lignin in the papermaking black liquor in an oven at 60°C for 8 hours to remove residual moisture, then mix it with other components of the above-mentioned A component and B component in the reactor, and reflux at 230°C for reaction After 1 hour, a heat conversion liquefied product was obtained.
[0049] Pour 60 parts of a mixture of dioxane and water with a volume ratio of 1:3 into the above thermochemical liquefaction product. Stir evenly and then centrifuge (5000 rev / min), and get the upper layer and the lower layer after standing and stratifying; the lower layer is glycerol solvent, which is recycled after vacuum distillation; the upper layer is phenolic chemicals and di The mixture of dioxane / water was removed by rotary evaporation to ob...
Embodiment 2
[0052] A component:
[0053] 100 grams of alkali lignin in papermaking black liquor
[0054] Aluminosilicate 4 g
[0055] Phenol 3 g
[0056] B component:
[0057] Glycerin 450 g
[0058] Dry the alkali lignin in the above weight parts of papermaking black liquor in an oven at 80°C for 8 hours to remove residual moisture, mix it with other components in the reactor, and react at 200°C for 0.5 hour to obtain thermal conversion liquefied product.
[0059] Pour 80 parts of a mixture of dioxane and water with a volume ratio of 1:6 into the above thermochemical liquefaction product. Stir evenly and then centrifuge (5000 rev / min), and get the upper layer and the lower layer after standing and stratifying; the lower layer is glycerol solvent, which is recycled after vacuum distillation; the upper layer is phenolic chemicals and di The mixture of dioxane / water was removed by rotary evaporation to obtain phenolic chemicals.
[0060] According to the GC-MS internal standard quant...
Embodiment 3
[0062] A component:
[0063] 100 grams of lignosulfonate in papermaking black liquor
[0064] Silicophosphoric acid 3 g
[0065] Phenol 5 g
[0066] B component:
[0067] Glycerin 400 g
[0068] Dry the lignosulfonate in the papermaking black liquor in an oven at 60°C for 8 hours to remove residual moisture, then mix it with other components in component A and component B in the reactor, and react at 230°C After 1 hour, a heat conversion liquefied product was obtained.
[0069] Pour 100 parts of a mixture of dioxane and water with a volume ratio of 1:10 into the above thermochemical liquefaction product. Stir evenly and then centrifuge (5000 rev / min), and get the upper layer and the lower layer after standing and stratifying; the lower layer is glycerol solvent, which is recycled after vacuum distillation; the upper layer is phenolic chemicals and di The mixture of dioxane / water was removed by rotary evaporation to obtain phenolic chemicals.
[0070] According to the GC...
PUM
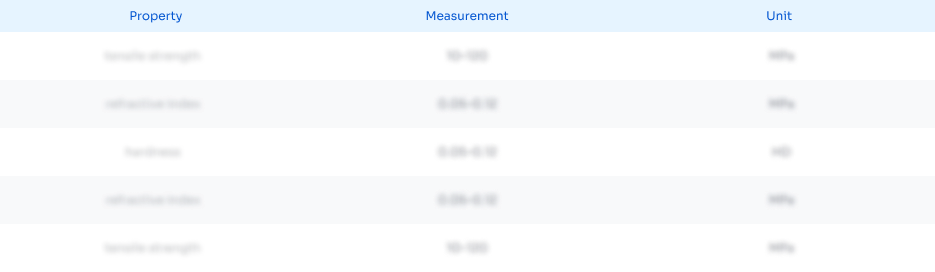
Abstract
Description
Claims
Application Information

- Generate Ideas
- Intellectual Property
- Life Sciences
- Materials
- Tech Scout
- Unparalleled Data Quality
- Higher Quality Content
- 60% Fewer Hallucinations
Browse by: Latest US Patents, China's latest patents, Technical Efficacy Thesaurus, Application Domain, Technology Topic, Popular Technical Reports.
© 2025 PatSnap. All rights reserved.Legal|Privacy policy|Modern Slavery Act Transparency Statement|Sitemap|About US| Contact US: help@patsnap.com