Iron and aluminum melting separation method for complicated and hard-dressing aluminum and iron intergrowth ore
An aluminum-iron symbiotic ore and separation method technology, applied in the field of metallurgy, can solve the problems of difficult separation, sluggishness, and difficulty in effectively separating iron and aluminum, and achieve the effects of reducing smelting costs, reducing CO2 emissions, and improving production efficiency.
- Summary
- Abstract
- Description
- Claims
- Application Information
AI Technical Summary
Problems solved by technology
Method used
Image
Examples
Embodiment 1
[0027] figure 1 An example flow chart of an aluminum-iron symgenetic ore based on pre-reduction-final reduction smelting according to an exemplary embodiment of the present invention is shown. like figure 1 As shown, this exemplary embodiment provides a method for smelting and separating iron and aluminum with complex distribution and refractory aluminum-iron paragenetic ore. The method includes: loading pellets of aluminum-iron paragenetic ore into the pre-reduction furnace 1, Then, carbon monoxide and / or hydrogen are introduced into the pre-reduction furnace 1 to partially reduce the pellets of the Al-Fe paragenetic ore, thereby forming pellets in which part of the iron oxide has been reduced, that is, partially metallized Al-Fe paragenetic ore. Then put the partially reduced pellets into the final reduction smelting furnace 2, further carry out final reduction by carbothermal high temperature, and use the difference in specific gravity between molten iron and alumina-conta...
Embodiment 2
[0029] According to an exemplary embodiment of the present invention, the iron-aluminum melting and separation method of complex embedded and refractory aluminum-iron paragenetic ore includes the following steps.
[0030] 1. Pre-reduction of iron-containing minerals. Add the aluminum-iron paragenetic ore powder or pellets directly from the upper part of the pre-reduction furnace 1 after mud washing, and at the same time, feed the reduction gas into the lower part of the pre-reduction furnace 1. The temperature range of the reduction gas is 750 ° C, and the reduction potential range is 0.6 . In the pre-reduction furnace 1, the iron-containing oxides in the aluminum-iron-containing symbiotic pellets undergo a reduction reaction with carbon monoxide or hydrogen in the reducing gas, and a part of the iron-containing minerals are reduced to obtain a direct reduction with a metallization rate of 40%. Metallized aluminum-iron symbiotic pellets. Here, preferably, considering the suf...
Embodiment 3
[0036] This embodiment is basically the same as Embodiment 2, except that the temperature range of the reducing gas fed into the lower part of the pre-reduction furnace 1 is 950°C, and the reduction potential range is 1.0; the metal of the pellets reduced by the preheating reduction furnace 1 The conversion rate is 90%; in the final reduction step, the fuel ratio of the fuel consisting of 40% lump coal and 60% pulverized coal by weight is about 950kg / tHM, and the basicity of the slag is CaO / SiO 2 =1.5, CaO / Al 2 o 3 =1.4, the secondary combustion rate is controlled to be about 45%, and the corresponding furnace slag temperature is about 1800°C; in the step of recovering alumina from the slag, the basicity of the slag is CaO / SiO 2 =2.1, CaO / Al 2 o 3 = 1.6, containing 98% by weight of calcium aluminate slag in the raw material, and the roasting time is 2 hours; in the high-temperature coal gas hydrogen-enriched reforming step, the coal gas temperature is 1850 ° C, and the mode...
PUM
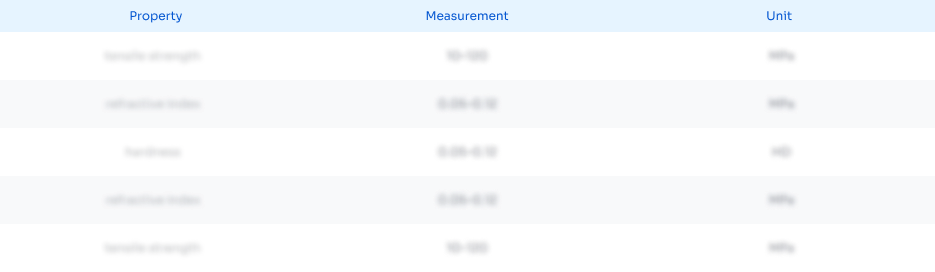
Abstract
Description
Claims
Application Information

- R&D Engineer
- R&D Manager
- IP Professional
- Industry Leading Data Capabilities
- Powerful AI technology
- Patent DNA Extraction
Browse by: Latest US Patents, China's latest patents, Technical Efficacy Thesaurus, Application Domain, Technology Topic, Popular Technical Reports.
© 2024 PatSnap. All rights reserved.Legal|Privacy policy|Modern Slavery Act Transparency Statement|Sitemap|About US| Contact US: help@patsnap.com