Z direction continuous carbon fiber prefabricated body
A carbon fiber and preform technology is applied in the field of improvement of existing continuous carbon fiber preform interlayer fabrics, and can solve the problems of high puncture difficulty, large damage to fibers in plane X and Y directions, and interface deposition at fiber lap joints. Achieve the effect of being beneficial to fiber strength, improving interlayer cohesion, and improving three-dimensional structural skeleton
- Summary
- Abstract
- Description
- Claims
- Application Information
AI Technical Summary
Problems solved by technology
Method used
Image
Examples
Embodiment 1
[0012] Example 1: Lamination without weft cloth, with continuous carbon fibers passing through the preform in the Z direction, and the size of the preform is 100×100×100mm 3 , The Z-direction fiber center distance is 2mm.
[0013] 12K carbon fiber is used to weave non-weft fabric, with a surface density of 240g / m 2 , Cut the non-weft fabric 100×100mm (the actual cutting size is enlarged by 10-20mm on each side), rotate the cut non-weft fabric layer by layer according to the direction of the long fiber 60 degrees and lay it to the required thickness to stop the lamination. On a 100×100mm platform, arrange a matrix of longitudinal steel needles at equal intervals of 2mm, with 50 steel needles in the X and Y directions, pass the matrix of steel needles through the laminated fiber body, and replace the steel needles one by one to penetrate the 12K longitudinal continuous carbon. The fibers are pressed and compacted to 22-24 layers / cm to form a weft-free puncture fabric with conti...
Embodiment 2
[0014] Embodiment 2: as embodiment 1, wherein when lamination does not have weft cloth, there is surface density 70g / m between every layer 2 Short carbon fiber mesh. The number of compacted layers is 16-18 layers / cm. See the attached table for performance indicators.
PUM
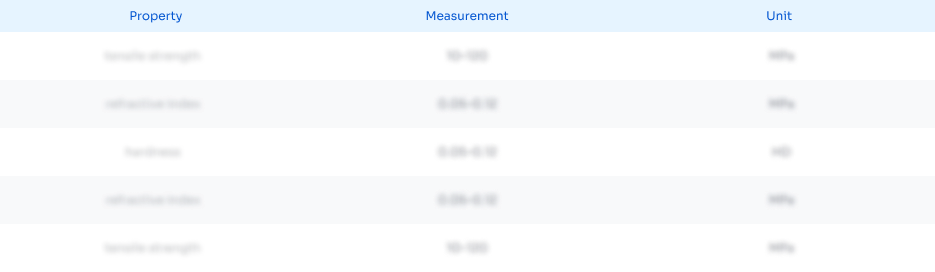
Abstract
Description
Claims
Application Information

- Generate Ideas
- Intellectual Property
- Life Sciences
- Materials
- Tech Scout
- Unparalleled Data Quality
- Higher Quality Content
- 60% Fewer Hallucinations
Browse by: Latest US Patents, China's latest patents, Technical Efficacy Thesaurus, Application Domain, Technology Topic, Popular Technical Reports.
© 2025 PatSnap. All rights reserved.Legal|Privacy policy|Modern Slavery Act Transparency Statement|Sitemap|About US| Contact US: help@patsnap.com