Method for preparing methyl chlorosilane by utilizing organosilicon high-boiling residues
A technology of methylchlorosilane and dimethyldichlorosilane, which is applied in the field of organosilicon monomer production technology, can solve the problems of low conversion rate and achieve the effect of improving conversion rate and good selectivity
- Summary
- Abstract
- Description
- Claims
- Application Information
AI Technical Summary
Problems solved by technology
Method used
Examples
Embodiment 1
[0023] Add 2500kg organosilicon high boiler and 50kg catalyst into the cracking kettle with packed fractionation tower. Heat up to 115°C with steam, and feed 25Nm 3 / h of hydrogen chloride gas (continuous), reaction under normal pressure. Start to react for 1 hour, continuously add high boiler 190kg / h in the cracking kettle, and simultaneously add catalyst 0.25kg / h, continuously react for 40 hours, and continuously collect condensed mixed monomers from the condenser. The conversion rate of its high boiling matter reaches 91.4%, and the main product consists of:
[0024] Monomethyldichlorosilane CH 3 HSiCl 20.87%
[0025] Monomethyltrichlorosilane CH 3 SiCl 3 16.06%
[0026] Dimethyldichlorosilane (CH 3 ) 2 SiCl 2 52.51%
[0027] Trimethylchlorosilane (CH 3 ) 3 SiCl 10.13%
Embodiment 2
[0029] Add 2500kg organosilicon high boilers and 62.5kg catalyst to the cracking kettle with packed fractionation tower. Heat up to 115°C with steam, and feed 25Nm 3 / h of hydrogen chloride gas (continuous), reaction under normal pressure. Start to react for 1.2 hours, continuously add high boiler 200kg / h in the cracking kettle, and add catalyst 0.3kg / h simultaneously, continuously react for 41 hours, and continuously collect condensed mixed monomers from the condenser. The conversion rate of its high boiling matter reaches 93.7%, and the main product consists of:
[0030] Monomethyldichlorosilane CH 3 HSiCl 19.02%
[0031] Monomethyltrichlorosilane CH 3 SiCl 3 12.70%
[0032] Dimethyldichlorosilane (CH 3 ) 2 SiCl 2 56.77%
[0033] Trimethylchlorosilane (CH 3 ) 3 SiCl 11.28%.
PUM
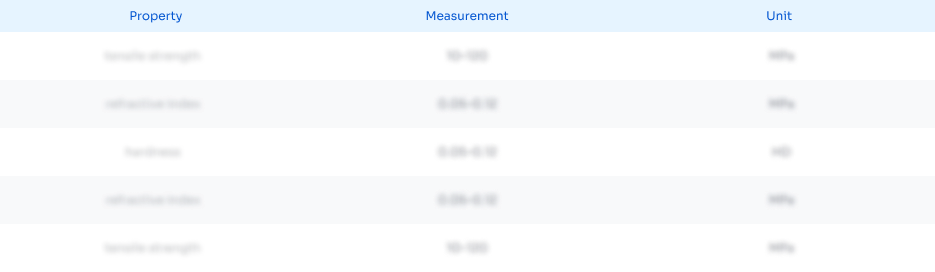
Abstract
Description
Claims
Application Information

- Generate Ideas
- Intellectual Property
- Life Sciences
- Materials
- Tech Scout
- Unparalleled Data Quality
- Higher Quality Content
- 60% Fewer Hallucinations
Browse by: Latest US Patents, China's latest patents, Technical Efficacy Thesaurus, Application Domain, Technology Topic, Popular Technical Reports.
© 2025 PatSnap. All rights reserved.Legal|Privacy policy|Modern Slavery Act Transparency Statement|Sitemap|About US| Contact US: help@patsnap.com