Segmental welding method for butt welding of raw material band steel joint plates of high-frequency straight welding tube
A straight seam welded pipe and segmented welding technology, which is applied in the field of metallurgical steel rolling, can solve the problems of cracking of the welding seam edge of the welded pipe, accelerated roller edge wear, and production stoppage.
- Summary
- Abstract
- Description
- Claims
- Application Information
AI Technical Summary
Problems solved by technology
Method used
Image
Examples
Embodiment Construction
[0028] The butt welding method of the butt welding of the raw material strip of the high-frequency longitudinal welded pipe of the present invention is described in conjunction with the accompanying drawings and embodiments.
[0029] The butt welding method of raw material strip butt welding of the high-frequency straight seam welded pipe of the present invention adopts the full plate width welding method instead of the segmented welding method for the current raw material strip butt welding. The method includes the following steps:
[0030] ① Segmentation
[0031] According to the width of the raw strip steel, it is divided into welded section and non-welded section. Sections A, C and E are welded sections, sections B and D are non-welded sections, and the two sides of the middle welded section C are equal sections A, A and E. Section B, section D, and section E, the welding length of section C in the middle welding section is 1 / 3L, the blank length of section B and D is 1 / 6...
PUM
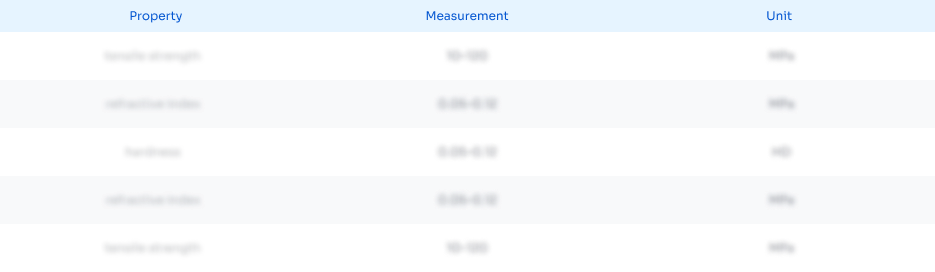
Abstract
Description
Claims
Application Information

- Generate Ideas
- Intellectual Property
- Life Sciences
- Materials
- Tech Scout
- Unparalleled Data Quality
- Higher Quality Content
- 60% Fewer Hallucinations
Browse by: Latest US Patents, China's latest patents, Technical Efficacy Thesaurus, Application Domain, Technology Topic, Popular Technical Reports.
© 2025 PatSnap. All rights reserved.Legal|Privacy policy|Modern Slavery Act Transparency Statement|Sitemap|About US| Contact US: help@patsnap.com