Industrial laser guidance AGV double-closed-loop control system and control method thereof
A technology of laser guidance and control system, used in conveyor control devices, conveyor objects, transportation and packaging, etc., can solve the problems of difficult to achieve accuracy, large inertia, slow path tracking speed, etc.
- Summary
- Abstract
- Description
- Claims
- Application Information
AI Technical Summary
Problems solved by technology
Method used
Image
Examples
Embodiment Construction
[0065] The laser-guided AGV used in this embodiment is a single-wheel drive rear-fork AGV transformed from a forklift, with a wheelbase of 1300 mm, a dead weight of 1 ton, and a rated lifting capacity of 800 kg. The front wheels are both driving wheels and are steering wheels, each controlled by an AC servo motor. like figure 1 As shown, the AGV is composed of a car body, a safety collision avoidance system, a walking steering system, a communication system, a two-position closed-loop control system and other auxiliary systems. Among them, the safety anti-collision system adopts the S3000 laser scanning safety device of German SICK company, which is fixed on the front end of the AGV car body and connected with the industrial computer through the communication line. The travel steering system consists of a servo motor, a reducer, and a travel steering mechanism. The communication system is a wireless local area network composed of a wireless network card and a wireless router...
PUM
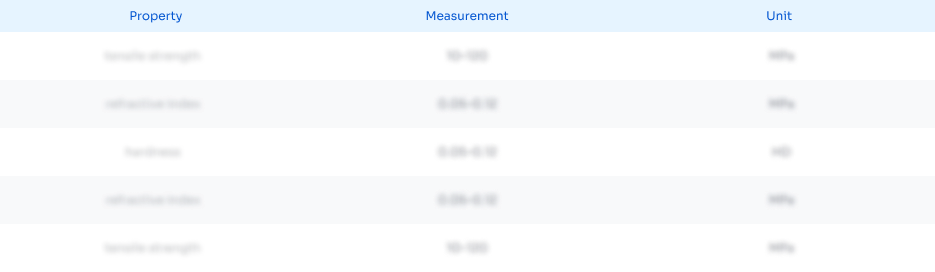
Abstract
Description
Claims
Application Information

- R&D
- Intellectual Property
- Life Sciences
- Materials
- Tech Scout
- Unparalleled Data Quality
- Higher Quality Content
- 60% Fewer Hallucinations
Browse by: Latest US Patents, China's latest patents, Technical Efficacy Thesaurus, Application Domain, Technology Topic, Popular Technical Reports.
© 2025 PatSnap. All rights reserved.Legal|Privacy policy|Modern Slavery Act Transparency Statement|Sitemap|About US| Contact US: help@patsnap.com