Device for unloading and buffering pull force
A pulling force and buffer element technology is applied in the field of static calibration devices of rocket engine thrust test systems, which can solve the problems of inability to achieve accurate return calibration, inability to automatically reset, and large impact on the moment of unloading, and achieve stable unloading, accurate return calibration, The effect of shock absorption
- Summary
- Abstract
- Description
- Claims
- Application Information
AI Technical Summary
Problems solved by technology
Method used
Image
Examples
Embodiment Construction
[0008] The specific implementation manner of the present invention is described in detail in conjunction with accompanying drawing and technical scheme, such as figure 1 , as shown in 2, the hydraulic cylinder support flange 6 is used as a support member. During installation, the base 3 is rigidly connected to the hydraulic cylinder support flange 6 through 6 evenly distributed bolts 7; On the small boss u of the flange, the bottom end is in contact with the inner spring support surface x; the cylinder 1 is directly loaded on the inner spring 4, and the top of the spring is in contact with the inner surface t of the upper end of the cylinder; the outer spring 5 is used as a buffer element Covered on the cylinder 1, the bottom end is in contact with the outer spring support surface d; the upper cover 2 is set on the cylinder 1 through the upper cover through hole r, and the upper cover 2 and the base 3 are connected together by threaded connection. And use a wrench to pre-tight...
PUM
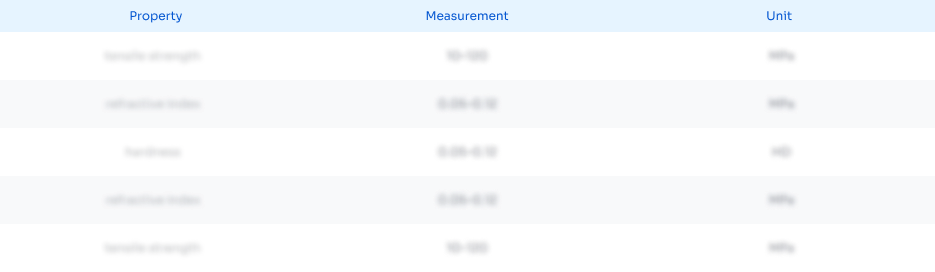
Abstract
Description
Claims
Application Information

- R&D Engineer
- R&D Manager
- IP Professional
- Industry Leading Data Capabilities
- Powerful AI technology
- Patent DNA Extraction
Browse by: Latest US Patents, China's latest patents, Technical Efficacy Thesaurus, Application Domain, Technology Topic, Popular Technical Reports.
© 2024 PatSnap. All rights reserved.Legal|Privacy policy|Modern Slavery Act Transparency Statement|Sitemap|About US| Contact US: help@patsnap.com