Plate-type pulsating heat pipe with double-side grooves
A pulsating heat pipe and double-sided groove technology, which is applied in heat exchange equipment, indirect heat exchangers, lighting and heating equipment, etc., can solve the problems that the application of pulsating heat pipes has not been paid enough attention, and the mechanism of pulsating heat transfer has not been uniformly explained. To achieve the effect of improving the uniformity of internal working fluid distribution and heat transfer, good heat transfer ability and good contact
- Summary
- Abstract
- Description
- Claims
- Application Information
AI Technical Summary
Problems solved by technology
Method used
Image
Examples
Embodiment 1
[0048] See attached figure 1 , 2 , 3, 4, the double-sided channel plate type pulsating heat pipe of the present invention comprises a shell 1 and a folded plate 2, the cross section of the shell 1 is a closed box with a rectangle; the folded plate 2 is composed of a periodic triangular shape The curved plate, the folded plate 2 is inserted in the shell 1, so that a plurality of pulsating channels 3 are formed between the folded plate 2 and the inner surface of the shell 1; the folded plate 2 The ribs are connected to the inner surface of the housing 1 through discontinuous spot welding spots 4, so that the adjacent channels are connected by micro seams 5; the housing 1 is closed, vacuumized and filled with distilled water as a working medium; The folded plate 2 is not flush with the ends 6 and 7 of the shell 1; the equivalent diameter of the pulsation channel 3 is 0.5-1mm; the shell and the folded plate are made of stainless steel; The length is 5-50 mm, and the width of the...
Embodiment 2
[0051] See attached Figure 5 , 6 , the double-sided channel plate type pulsating heat pipe of the present invention includes a housing 1 and a folded plate 2, the cross section of the housing 1 is a rectangular closed box; the folded plate 2 is a curved plate made of a periodic sine wave shape , the shell 1 and the folded plate 2 are integrally stretched or extruded, the folded plate 2 is in the shell 1, and the gap between the folded plate 2 and the inner surface of the shell 1 A plurality of pulsating channels 3 are formed between them; the housing 1 is closed, vacuumized and filled with working fluid R123; the flap 2 is not flush with one end of the housing 1; the equivalent diameter of the channels is 0.5-3.5 mm; the shell and the folding plate are made of aluminum alloy.
PUM
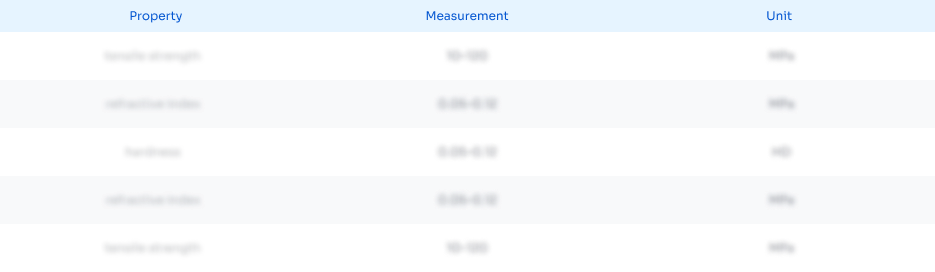
Abstract
Description
Claims
Application Information

- R&D Engineer
- R&D Manager
- IP Professional
- Industry Leading Data Capabilities
- Powerful AI technology
- Patent DNA Extraction
Browse by: Latest US Patents, China's latest patents, Technical Efficacy Thesaurus, Application Domain, Technology Topic, Popular Technical Reports.
© 2024 PatSnap. All rights reserved.Legal|Privacy policy|Modern Slavery Act Transparency Statement|Sitemap|About US| Contact US: help@patsnap.com