Preparation process of photo-resist cleaning liquid
A preparation process and cleaning fluid technology, applied in the direction of photosensitive material processing, etc., can solve the problems of low production capacity and difficult to control the cleanliness of photoresist cleaning fluid, so as to improve production efficiency and production capacity, improve product competitiveness, and reduce production costs. Effect
- Summary
- Abstract
- Description
- Claims
- Application Information
AI Technical Summary
Problems solved by technology
Method used
Image
Examples
Embodiment 1
[0045] Example 1 Preparation process of a novel photoresist cleaning solution with high cleanliness The preparation process:
[0046] (1) Confirm that all raw materials have passed the test and are in place; check and correct the measurement equipment, production equipment, and pure water supply system to ensure that they meet the specifications and requirements;
[0047] (2) Intermediate premix 1: Add 1030 kg of dimethyl sulfoxide, 900 kg of pure water and 750 kg of dipropylene glycol methyl ether into the finished product mixing tank through the feeding system, and turn on until the mixing is uniform, and the total number of particles is detected (LPC) and trace metal ion residues are tested for use;
[0048]Intermediate premix 2: Add 200 kilograms of triethylamine to the mixing tank 1, add 120 kilograms of pentamethyldiethylenetriamine at a stirring speed of 120 rpm, stir until the mixture is uniform, and continue to stir Slowly add 50 kg of iminodiacetic acid at low tempe...
Embodiment 2
[0053] Example 2 Preparation process of a novel photoresist cleaning solution with high cleanliness Preparation process:
[0054] (1) Confirm that all raw materials have passed the test and are in place; check and correct the measurement equipment, production equipment, and pure water supply system to ensure that they meet the specifications and requirements;
[0055] (2) Intermediate premix 1: Add 1030 kg of dimethyl sulfoxide, 900 kg of pure water and 750 kg of dipropylene glycol methyl ether to the finished product mixing tank through the feeding system, stir and mix evenly, slowly add 140 kg of 40% fluorine Aqueous solution of ammonium chloride, stirred until the mixture is completely uniform, after passing the detection of the total number of large particles, trace metal ion residues and fluoride ion concentration, it is ready to use;
[0056] Intermediate premix 2: Add 200 kilograms of triethylamine to the mixing tank 1, add 120 kilograms of pentamethyldiethylenetriamine...
Embodiment 3
[0060] Example 3 Preparation process of a novel photoresist cleaning solution with high cleanliness Preparation process:
[0061] (1) Confirm that all raw materials have passed the test and are in place; check and correct the measurement equipment, production equipment, and pure water supply system to ensure that they meet the specifications and requirements;
[0062] (2) Intermediate premix 1: Add 1030 kg of dimethyl sulfoxide, 900 kg of pure water and 750 kg of dipropylene glycol methyl ether into the finished product mixing tank through the feeding system, and turn on until the mixing is uniform, and the total number of particles is detected (LPC) and trace metal ion residues are tested for use;
[0063] Intermediate premix 2: Add 200 kilograms of triethylamine to the mixing tank 1, and add 120 kilograms of pentamethyldiethylenetriamine at a stirring speed of 120 rpm, and stir until uniformly mixed. It is ready to be used after the detection of the total number of particle...
PUM
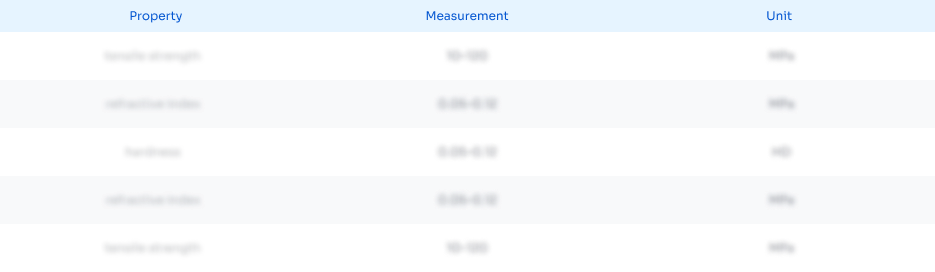
Abstract
Description
Claims
Application Information

- R&D Engineer
- R&D Manager
- IP Professional
- Industry Leading Data Capabilities
- Powerful AI technology
- Patent DNA Extraction
Browse by: Latest US Patents, China's latest patents, Technical Efficacy Thesaurus, Application Domain, Technology Topic, Popular Technical Reports.
© 2024 PatSnap. All rights reserved.Legal|Privacy policy|Modern Slavery Act Transparency Statement|Sitemap|About US| Contact US: help@patsnap.com