Method for preparing functional carbon fibers
A carbon fiber and carbonization technology, applied in the field of preparation of functionalized carbon fiber, can solve the problems of increased interface rigidity, low reactivity, low interface bonding strength, etc. The effect of shear strength
- Summary
- Abstract
- Description
- Claims
- Application Information
AI Technical Summary
Problems solved by technology
Method used
Image
Examples
Embodiment l
[0026] Example 1: Multi-walled carbon nanotubes (OD<8nm) and carbon fibers prepared by the arc discharge method are used as initial raw materials. After purification, acidification and amination, the multi-walled carbon nanotubes react with acidified carbon fibers. After a certain period of reaction , and then add decyl diamine to the system to fully aminate the carboxyl groups that have not completely reacted with the aminated carbon nanotubes on the surface of the carbon fiber, and the carbon fiber surface obtained is grafted with carbon nanotubes and decyl diamine.
[0027] Step (1): In a 250mL single-necked round bottom flask equipped with a stirrer, add 1.1g of dried multi-walled carbon nanotube raw material and 100mL, 20% nitric acid solution, treat it under 1kHz ultrasonic wave for 24 hours, and then heat to 20°C, react for 48 hours, filter with ψ0.45μm polytetrafluoroethylene microfiltration membrane, wash with deionized water 3-10 times until neutral, and vacuum dry at...
Embodiment 2
[0034] Example 2: Single-walled carbon nanotubes (OD<8nm) prepared by chemical vapor deposition are used as the initial raw material. After purification, acidification and amination, the single-walled carbon nanotubes react with acidified carbon fibers. After a certain period of time, Hexamethylenediamine is then added to the system to fully aminate the carboxyl groups that have not completely reacted with the aminated carbon nanotubes on the surface of the carbon fibers, and the obtained carbon fibers are grafted with carbon nanotubes and hexamethylenediamine.
[0035] Step (1): In a 500mL single-neck round bottom flask equipped with a magnetic stirring rotor, add 3.1g of dried single-walled carbon nanotube raw material, 250mL, 20% weight concentration of sulfuric acid, and use 120kHz ultrasonic treatment for 12 hours, Then heated to 180°C, reacted for 48 hours, filtered with ψ0.8μm polytetrafluoroethylene microfiltration membrane, washed repeatedly with deionized water until ...
Embodiment 3
[0041] Example 3: Single-walled carbon nanotubes (OD<8nm) prepared by laser evaporation method were used as the initial raw material. After purification, acidification and amination, the single-walled carbon nanotubes reacted with acidified carbon fibers. Ethylenediamine is added to the system to fully aminate the carboxyl groups that have not completely reacted with the aminated carbon nanotubes on the surface of the carbon fibers, and the obtained carbon fibers are grafted with carbon nanotubes and ethylenediamine.
[0042] Step (1): In the 1000mL single-neck round bottom flask that magnetic stirring rotor has been housed, add 10g single-walled carbon nanotube raw material and 250mL, 20% weight concentration sulfuric acid solution, use 120kHz ultrasonic treatment for 80 hours, then heat and in Stir and reflux at 150°C, react for 48 hours, filter with ψ0.8μm polytetrafluoroethylene microfiltration membrane, wash repeatedly with deionized water for 2-10 times until neutral, and...
PUM
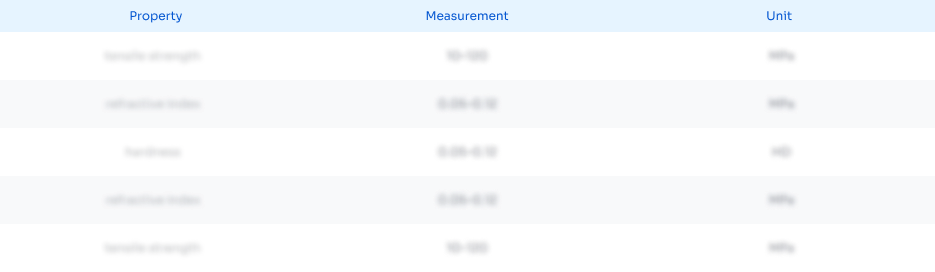
Abstract
Description
Claims
Application Information

- R&D
- Intellectual Property
- Life Sciences
- Materials
- Tech Scout
- Unparalleled Data Quality
- Higher Quality Content
- 60% Fewer Hallucinations
Browse by: Latest US Patents, China's latest patents, Technical Efficacy Thesaurus, Application Domain, Technology Topic, Popular Technical Reports.
© 2025 PatSnap. All rights reserved.Legal|Privacy policy|Modern Slavery Act Transparency Statement|Sitemap|About US| Contact US: help@patsnap.com