Fine grain casting tungsten carbide continuous production furnace
A casting tungsten carbide, fine-grained technology, applied in the direction of carbide, tungsten/molybdenum carbide, liquid droplet granulation, etc., can solve the problem that it is not suitable for high-end hard surface spraying materials, casting tungsten carbide solution cooling speed is slow, Poor working conditions, etc.
Inactive Publication Date: 2011-06-15
株洲弗拉德科技有限公司
View PDF6 Cites 0 Cited by
- Summary
- Abstract
- Description
- Claims
- Application Information
AI Technical Summary
Problems solved by technology
At present, in the cemented carbide industry, the production of cast tungsten carbide generally adopts a horizontal carbon tube furnace. The mixture of tungsten powder and tungsten carbide powder is packed in a boat, and the boat is placed in the In the horizontal carbon tube furnace, the mixture is heated to a liquid state to form a cast tungsten carbide solution, and then the boat is pushed out of the furnace, and the operator pours the high-temperature cast tungsten carbide solution of about 2800 degrees into the In the cooling container, cast tungsten carbide products are obtained after cooling. Practice has proved that this one-time pouring method makes the solution form larger lumps in the cooling container, resulting in slow cooling of the casting tungsten carbide solution, and the cast tungsten carbide obtained after cooling. The crystalline phase of tungsten carbide products is coarse dendritic grain structure (that is, "coarse grain cast tungsten carbide"), rather than fine grain cast tungsten carbide with fine grain structure, which is not suitable for high-end hard surface spraying materials
In addition, this method of intermittent heating and pouring outside the furnace also has disadvantages such as poor working conditions and serious oxidation of materials.
Method used
the structure of the environmentally friendly knitted fabric provided by the present invention; figure 2 Flow chart of the yarn wrapping machine for environmentally friendly knitted fabrics and storage devices; image 3 Is the parameter map of the yarn covering machine
View moreImage
Smart Image Click on the blue labels to locate them in the text.
Smart ImageViewing Examples
Examples
Experimental program
Comparison scheme
Effect test
Embodiment Construction
the structure of the environmentally friendly knitted fabric provided by the present invention; figure 2 Flow chart of the yarn wrapping machine for environmentally friendly knitted fabrics and storage devices; image 3 Is the parameter map of the yarn covering machine
Login to View More PUM
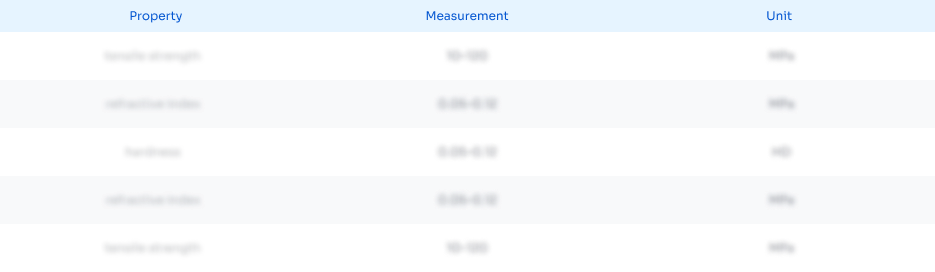
Abstract
The invention relates to a fine grain casting tungsten carbide continuous production furnace. The production furnace is divided into three parts, namely a feeding device, an upper furnace body and a lower furnace body. the integral structure of the production furnace is a vertical structure. The production furnace contains the feeding device, the upper furnace body, a conical throwing disk, the lower furnace body, a discharging pipe, a gas inlet nozzle and an observation pipe. The production furnace is characterized in that the inside of the upper furnace body is provided with a round graphite crucible with a central small hole at the bottom; and the conical throwing disk is arranged below the graphite crucible, the conical throwing disk is near the graphite crucible and performs high-speed circular motion around the axis, and the axis is parallel to the central vertical line of the graphite crucible to maintain a proper horizontal distance. Under the centrifugal force of the conical throwing disk, the solution is broken to tiny particles and the tiny particles are thrown on the inner wall of a water-cooled sandwich cylinder, thus the high temperature solution can be fast cooled and the fine grain casting tungsten carbide product with fine grains can be obtained; and the production furnace has high cooling speed, low degree of oxidation of material, low energy consumption and high yield, and can be used to realize continuous production operation.
Description
Fine-grain cast tungsten carbide continuous production furnace technical field The invention relates to a fine-grain cast tungsten carbide continuous production furnace, in particular to a fine-grain cast tungsten carbide continuous production furnace capable of continuously preparing cast tungsten carbide with a fine-grain structure in the cemented carbide industry. technical background At present, in the cemented carbide industry, the production of cast tungsten carbide generally adopts a horizontal carbon tube furnace. The mixture of tungsten powder and tungsten carbide powder is packed in a boat, and the boat is placed in the In the horizontal carbon tube furnace, the mixture is heated to a liquid state to form a cast tungsten carbide solution, and then the boat is pushed out of the furnace, and the operator pours the high-temperature cast tungsten carbide solution of about 2800 degrees into the In the cooling container, cast tungsten carbide products are obtained afte...
Claims
the structure of the environmentally friendly knitted fabric provided by the present invention; figure 2 Flow chart of the yarn wrapping machine for environmentally friendly knitted fabrics and storage devices; image 3 Is the parameter map of the yarn covering machine
Login to View More Application Information
Patent Timeline

IPC IPC(8): C01B31/34B01J2/02C01B32/949
Inventor 言伟雄
Owner 株洲弗拉德科技有限公司
Features
- R&D
- Intellectual Property
- Life Sciences
- Materials
- Tech Scout
Why Patsnap Eureka
- Unparalleled Data Quality
- Higher Quality Content
- 60% Fewer Hallucinations
Social media
Patsnap Eureka Blog
Learn More Browse by: Latest US Patents, China's latest patents, Technical Efficacy Thesaurus, Application Domain, Technology Topic, Popular Technical Reports.
© 2025 PatSnap. All rights reserved.Legal|Privacy policy|Modern Slavery Act Transparency Statement|Sitemap|About US| Contact US: help@patsnap.com