Coprecipitation Cd/Al (Cadmium / Aluminum) catalyst and application of catalyst for catalyzing and synthesizing 2,6-naphthalenedicarboxylic acid
A naphthalene dicarboxylic acid and co-precipitation technology, which is applied in the direction of physical/chemical process catalysts, carboxylate preparation, chemical instruments and methods, etc., can solve the problems of low catalytic activity and small specific surface area, and achieve high natural purity and specific surface area. The effect of large surface area and low production cost
- Summary
- Abstract
- Description
- Claims
- Application Information
AI Technical Summary
Problems solved by technology
Method used
Image
Examples
experiment example 1
[0033] At 80°C, add dropwise a mixed solution of 300 mL of 0.8 mol / L cadmium nitrate aqueous solution and 0.8 mol / L aluminum nitrate aqueous solution in 200 mL of 1.0 mol / L sodium carbonate aqueous solution (wherein the cadmium nitrate aqueous solution and the aluminum nitrate aqueous solution The volume ratio is 19:1), stir quickly, add dropwise to pH = 4, then back drop sodium carbonate solution to pH = 9, and age at 80°C for 30min, filter, wash, dry the filter residue at 120°C for 12h, cool to room temperature, then raised from room temperature to 500 °C at 2 °C / min, after calcination for 3 hours, cooled naturally to room temperature, taken out and kept dry. Obtain coprecipitation Cd / Al=95 / 5 catalyzer 26.3g at last, do XRD characterization to the catalyzer after drying, the peak position that obtains is consistent with the peak position of standard cadmium oxide, aluminum oxide (see attachment figure 1 ).
experiment example 2
[0035] At 80°C, add dropwise a mixed solution of 300 mL of 0.8 mol / L cadmium nitrate aqueous solution and 0.8 mol / L aluminum nitrate aqueous solution in 200 mL of 1.0 mol / L sodium carbonate aqueous solution (wherein the cadmium nitrate aqueous solution and the aluminum nitrate aqueous solution The volume ratio is 7:3), stirring quickly, adding dropwise to pH=4, then back-dropping 1.0mol / L sodium carbonate solution to pH=9, aging at 80°C for 30min, filtering, washing, and filtering the filter residue at 120 Dry at ℃ for 12 hours, cool to room temperature, then raise from room temperature to 550℃ at 2℃ / min, after calcining for 3h, cool to room temperature naturally, take it out and keep it dry. Finally, 18.5 g of the co-precipitated Cd / Al=70 / 30 catalyst was obtained, and XRD was performed on the dried catalyst, and the peak positions obtained were consistent with those of standard cadmium oxide and aluminum oxide.
experiment example 3
[0037]At 80°C, add dropwise a mixed solution of 300 mL of 0.8 mol / L cadmium nitrate aqueous solution and 0.8 mol / L aluminum nitrate aqueous solution in 200 mL of 1.0 mol / L sodium carbonate aqueous solution (wherein the cadmium nitrate aqueous solution and the aluminum nitrate aqueous solution The volume ratio is 19:1), stir quickly, add dropwise to pH = 4, then back drop sodium carbonate solution to pH = 9, and age at 80°C for 30min, filter, wash, dry the filter residue at 120°C for 12h, cool to room temperature, and then raised from room temperature to 650 °C at 2 °C / min, after calcination for 3 hours, naturally cooled to room temperature, taken out and kept dry. Finally, 25.5 g of the co-precipitated Cd / Al=95 / 5 catalyst was obtained, and XRD was performed on the dried catalyst, and the peak positions obtained were consistent with those of standard cadmium oxide and aluminum oxide.
PUM
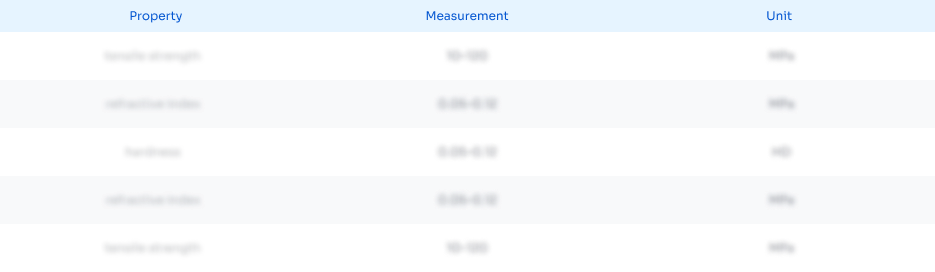
Abstract
Description
Claims
Application Information

- Generate Ideas
- Intellectual Property
- Life Sciences
- Materials
- Tech Scout
- Unparalleled Data Quality
- Higher Quality Content
- 60% Fewer Hallucinations
Browse by: Latest US Patents, China's latest patents, Technical Efficacy Thesaurus, Application Domain, Technology Topic, Popular Technical Reports.
© 2025 PatSnap. All rights reserved.Legal|Privacy policy|Modern Slavery Act Transparency Statement|Sitemap|About US| Contact US: help@patsnap.com