Novel dry-method degumming method for abandoned oil
A degumming method, a new technology, applied in the direction of fat oil/fat refining, fat production, etc., can solve the problems of emulsification, hygroscopic hydrolysis, bumping, etc., and achieve the effect of improving oil quality, simple operating conditions, and saving water resources
- Summary
- Abstract
- Description
- Claims
- Application Information
AI Technical Summary
Problems solved by technology
Method used
Image
Examples
Embodiment 1
[0025] 500Kg of crude waste oil that has passed through the fence is pumped into the reaction kettle through the pipeline, heated to 110 ° C ~ 115 ° C, the vacuum degree is controlled at 0.090 MPa, and the stirring speed is 105 r / min. After 40 minutes, there is no bumping phenomenon of the material, and there is no phenomenon of oil on the surface of the oil layer. Bubbles are generated. Cool down to 100°C, add 1.0kg of acid reagent in oil, reduce the stirring speed after adding acid, control the stirring speed at 50r / min, the reaction temperature is 100°C, and the reaction time is 70min. After completion, 5Kg of adsorbent was added, the vacuum degree was 0.090Mpa, and the temperature was 120°C under continuous stirring conditions for 75min, and the stirring speed was controlled at 60r / min. Slightly lower the temperature to 100°C, pass through a filter press, and enter the next reaction kettle. The raw material quality after degumming is as follows:
[0026]
Embodiment 2
[0032] 2000Kg of crude waste oil that has passed through the fence is pumped into the reaction kettle through the pipeline, heated to 110 ° C ~ 115 ° C, the vacuum degree is controlled at 0.090 MPa, the stirring speed is 110 r / min, and there is no bumping phenomenon of the material after 40 minutes. Bubbles are generated. Cool down to 100°C, add 1.0kg of acid reagent in oil, reduce the stirring speed after adding acid, control the stirring speed at 60r / min, the reaction temperature is 100°C, and the reaction time is 55min. After completion, 5Kg of adsorbent was added, the vacuum degree was 0.090Mpa, and the temperature was 120°C under continuous stirring for 80 minutes, and the stirring speed was controlled at 60r / min. Slightly lower the temperature to 100°C, pass through a filter press, and enter the next reaction kettle. The raw material quality after degumming is as follows:
[0033]
Embodiment 3
[0035] 1000Kg of crude waste oil that has passed through the fence is pumped into the reaction kettle through the pipeline, heated to 110℃~115℃, the vacuum degree is controlled at 0.090MPa, the stirring speed is 105r / min, after 40min the material has no bumping phenomenon, and the surface of the oil layer has no Bubbles are generated. Cool down to 100°C, add 1.0kg of acid reagent in oil, reduce the stirring speed after adding acid, control the stirring speed at 55r / min, the reaction temperature is 100°C, and the reaction time is 85min. After completion, 5Kg of adsorbent was added, the vacuum degree was 0.090Mpa, and the temperature was 120°C under the condition of continuous stirring for 50min, and the stirring speed was controlled at 60r / min. Slightly lower the temperature to 100°C, pass through a filter press, and enter the next reaction kettle. The raw material quality after degumming is as follows:
[0036]
PUM
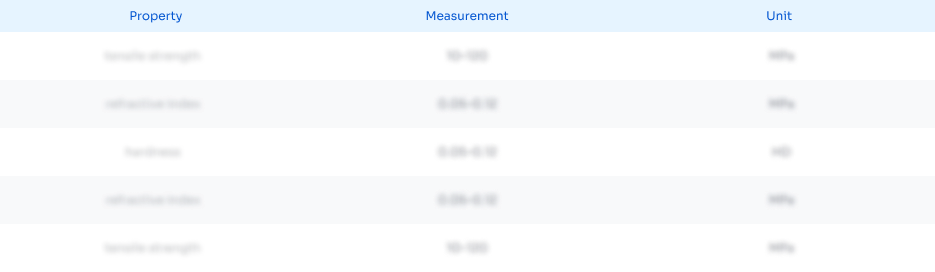
Abstract
Description
Claims
Application Information

- R&D Engineer
- R&D Manager
- IP Professional
- Industry Leading Data Capabilities
- Powerful AI technology
- Patent DNA Extraction
Browse by: Latest US Patents, China's latest patents, Technical Efficacy Thesaurus, Application Domain, Technology Topic, Popular Technical Reports.
© 2024 PatSnap. All rights reserved.Legal|Privacy policy|Modern Slavery Act Transparency Statement|Sitemap|About US| Contact US: help@patsnap.com