Areal heating wafer table and heating method for laser heat treatment device
A laser heat treatment and zone heating technology, applied in electrical components, semiconductor/solid-state device manufacturing, circuits, etc., can solve the problems of wafer surface topography damage, large temperature gradient, etc., to reduce adverse effects, reduce temperature gradient, The effect of reducing the temperature distribution gradient
- Summary
- Abstract
- Description
- Claims
- Application Information
AI Technical Summary
Problems solved by technology
Method used
Image
Examples
Embodiment Construction
[0019] The invention provides a partition auxiliary heating stage and a partition heating method used in laser heat treatment of semiconductor wafers. The structure of the table partition and independent heating control of each area is as follows: figure 1 , figure 2 shown.
[0020] exist figure 1 In the process, the chip stage is first divided into different unit areas 1, and the different unit areas are separated by heat insulating material 2, and a heating source with independent control of heating power is placed under each heating unit area 1 of the chip stage 3. Form a wafer stage with independent heating control for each unit area; an additional sub-high temperature buffer zone 7 is introduced between the high temperature area 5 introduced by laser heat treatment and the low temperature substrate preheating area 6 . The heating can be controlled independently in each zone, and the configuration of the heaters in each zone, such as figure 2 shown. The specific way...
PUM
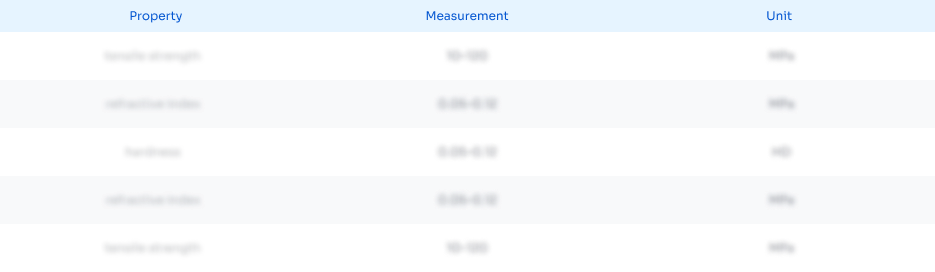
Abstract
Description
Claims
Application Information

- Generate Ideas
- Intellectual Property
- Life Sciences
- Materials
- Tech Scout
- Unparalleled Data Quality
- Higher Quality Content
- 60% Fewer Hallucinations
Browse by: Latest US Patents, China's latest patents, Technical Efficacy Thesaurus, Application Domain, Technology Topic, Popular Technical Reports.
© 2025 PatSnap. All rights reserved.Legal|Privacy policy|Modern Slavery Act Transparency Statement|Sitemap|About US| Contact US: help@patsnap.com