Special equipment and preparation method of contact strip compound solder for low-voltage appliance
A technology of low-voltage electrical appliances and special equipment, which is applied in the field of manufacturing complex solder contact strips, can solve the problems of energy utilization rate of only 40%, reduce the contact resistance of the welding surface, and uneven thickness of the solder layer, etc., to achieve guaranteed The effect of energy utilization, low contact resistance, uniform and stable solder layer
- Summary
- Abstract
- Description
- Claims
- Application Information
AI Technical Summary
Problems solved by technology
Method used
Image
Examples
preparation example Construction
[0028] A method for preparing a re-solder strip for low-voltage electrical appliances, the steps are as follows:
[0029] 1) First, according to the material properties and dimensions of the solder strip 18 and the contact strip 19, different front and rear roller electrode pairs (4, 5, 10, 11) are made;
[0030] 2) The strips (18, 19) processed to the predetermined size are placed on the unwinding device (2, 1);
[0031] 3) The strips (18, 19) are treated with surface degreasing and surface inclusions through the strip surface treatment device 3;
[0032] 4) The re-solder equipment is closed and loosened, if attached figure 1 As shown, the strip passes through the front roller electrode pair (4, 5), the rear roller electrode pair (10, 11), the rear roller electrode pair cooling water (13, 14), and the air inlet 8 of the re-solder atmosphere protection device. is closed;
[0033] 5) Press the strip (18, 19) onto the lower roller electrode (4, 10) through the upper roller el...
Embodiment 1
[0040] The contact material is AgCdO12, and the cross-section of the strip is 44mmX1mm; the solder strip is BCu80AgP, and the cross-section of the strip is 40X0.08mm. The specific re-soldering steps are as follows:
[0041] 1) Make copper-tungsten roller electrodes, and the front and rear roller electrodes have a uniform specification of Φ100mmX50mm;
[0042]2) The contact strip 19 is placed on the unwinding device 1, and the solder strip 18 is placed on the unwinding device 2;
[0043] 3) The strip (18, 19) passes through the strip surface treatment device 3, the front roller electrode pair (4, 5), the re-solder atmosphere protection device 7, the rear roller electrode pair (10, 11), and the strip surface treatment Device 3, cylinders (6, 12) for upper roller electrodes, air inlet 8 of re-solder atmosphere protection device, rear roller electrode pair (10, 11), and rear roller electrode pair cooling water (13, 14) are all closed and loose state;
[0044] 4) Press the strip ...
Embodiment 2
[0049] The contact material is AgSnO 2 (12), the strip cross-section specification is 52mmX1.8mm; the solder strip is BAg65CuP, and the strip section specification is 50X0.1mm. The specific re-solder steps are as follows:
[0050] 1) Make copper-tungsten roller electrodes, and the front and rear roller electrodes have a uniform specification of Φ300mmX60mm;
[0051] 2) The contact strip 19 is placed on the unwinding device 1, and the solder strip 18 is placed on the unwinding device 2;
[0052] 3) The strip (18, 19) passes through the strip surface treatment device 3, the front roller electrode pair (4, 5), the re-solder atmosphere protection device 7, the rear roller electrode pair (10, 11), and the strip surface treatment Device 3, cylinders (6, 12) for upper roller electrodes, air inlet 8 of re-solder atmosphere protection device, rear roller electrode pair (10, 11), and rear roller electrode pair cooling water (13, 14) are all closed and loose state;
[0053] 4) Press t...
PUM
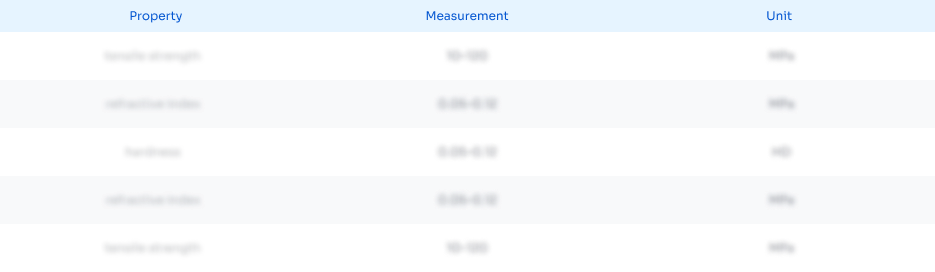
Abstract
Description
Claims
Application Information

- Generate Ideas
- Intellectual Property
- Life Sciences
- Materials
- Tech Scout
- Unparalleled Data Quality
- Higher Quality Content
- 60% Fewer Hallucinations
Browse by: Latest US Patents, China's latest patents, Technical Efficacy Thesaurus, Application Domain, Technology Topic, Popular Technical Reports.
© 2025 PatSnap. All rights reserved.Legal|Privacy policy|Modern Slavery Act Transparency Statement|Sitemap|About US| Contact US: help@patsnap.com