Method for optimizing circulating cooling water convey system
A technology for circulating cooling water and conveying systems, which is applied in pipeline systems, mechanical equipment, gas/liquid distribution and storage, etc., and can solve problems such as low system efficiency
- Summary
- Abstract
- Description
- Claims
- Application Information
AI Technical Summary
Problems solved by technology
Method used
Image
Examples
Embodiment 1
[0052] Optimization method of 1080 blast furnace circulating medium pressure circulating cooling water system in a steel plant.
[0053] Data collection of each link of the circulating cooling water system: a total of 3 water pumps (2 for use and 1 for standby all year round), parallel operation, water pump model 500S-100TD, rated flow rate 2422m 3 / h, rated head 81.8m, rotating speed 980r / min, matching motor model YJK5004-6, rated power 800KW, voltage 6KV, rated current 97.2A, cosΦ=0.83. Go to the power distribution room to find out that the actual operating current is 75A and 67.5A, and the actual operating voltage is 6300V. The calculated actual operating power is: 679KW and 611KW respectively. The pump inlet and upper tower valves are fully open, the internal thread gate valve of the pump outlet is opened 1 / 8, the outlet check valve cannot be fully opened, the pipe diameter is DN600, the liquid level of the pool is 2.8m, and the pump room is located on the large ground. ...
Embodiment 2
[0061] Optimization of circulating cooling water system of acetic anhydride plant in a chemical fertilizer plant:
[0062] Data collection of each link of the circulating cooling water system: 4 water pumps (2 for use and 2 for standby), with a flow rate of 2200m 3 / h, rated head 60.5m, speed 1450r / min, rated power of supporting motor 500KW, voltage 6KV, rated current 60A, actual operating current 41A. The liquid level of the pool is 0.6m, the inlet and outlet valves of the pump are fully opened, the butterfly valve of the water supply main pipe is opened at 60°, the butterfly valve of the return water main pipe is opened at 20°, the outlet pressure of the pump is 0.32Mpa, and the impeller of the water pump is seriously corroded.
[0063] Correspondingly eliminate the valve loss, local circulation, high and low pressure mixing, pipeline blockage and unnecessary losses in the system, and replace the pump model at the same time: draw the pipeline characteristic map, find out the...
Embodiment 3
[0065] System optimization of circulating cooling water system in a pharmaceutical factory:
[0066] Data collection of each link of the circulating cooling water system, recording system field data: a total of 4 units, parallel operation, 3 units in summer and 2 units in winter, water pump model 20SH-13, rated flow 3168m 3 / h, rated head 47.4m, rotating speed 970r / min, matching motor model Y500-6, rated power 560KW, voltage 10KV, rated current 39.2A. Go to the power distribution room to find out that the actual operating current is 27.5A. The calculated actual operating power is: 405KW. The pump inlet, outlet and upper tower valves are fully open, the liquid level of the pool is 1.8m, and the pump room is located on the ground. The outlet pressure of the water pump is 0.27MPa, and the system supplies heat exchange equipment and process water in each workshop. The highest water point of the terminal equipment is 23m, and the total flow is 7711m 3 / h.
[0067] Corresponding...
PUM
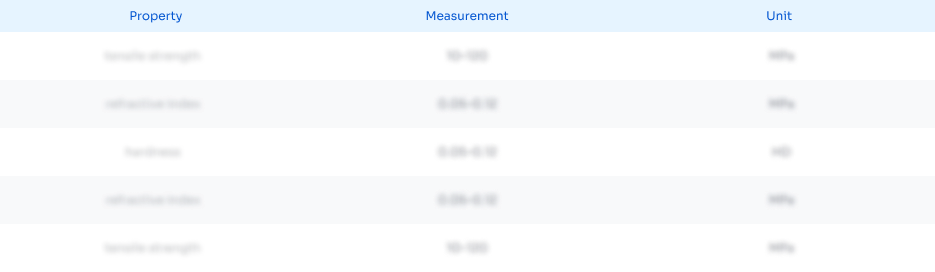
Abstract
Description
Claims
Application Information

- R&D
- Intellectual Property
- Life Sciences
- Materials
- Tech Scout
- Unparalleled Data Quality
- Higher Quality Content
- 60% Fewer Hallucinations
Browse by: Latest US Patents, China's latest patents, Technical Efficacy Thesaurus, Application Domain, Technology Topic, Popular Technical Reports.
© 2025 PatSnap. All rights reserved.Legal|Privacy policy|Modern Slavery Act Transparency Statement|Sitemap|About US| Contact US: help@patsnap.com