Manufacturing method of film split polytetrafluoroethylene fibers
A technology of polytetrafluoroethylene and a manufacturing method, which is applied in the directions of fiber processing, textile and papermaking, single-component halogenated hydrocarbon rayon, etc., can solve the problem of unstable fiber strength and strength uniformity index, fiber elongation at break The indicators are unstable and the weight of fixed-length fibers is not easy to reduce, so as to achieve the effects of improved performance, thin fiber diameter and low production cost
- Summary
- Abstract
- Description
- Claims
- Application Information
AI Technical Summary
Problems solved by technology
Method used
Image
Examples
Embodiment 1
[0045] Mix polytetrafluoroethylene micropowder and aviation kerosene at a weight ratio of 39:11; stir the mixed raw materials at a stirring speed of 2r / min, a stirring temperature of 20°C, and a stirring time of 90 minutes, so that the raw materials are fully mixed.
[0046] Place the stirred mixed raw materials at a temperature of 40°C and let them stand for 48 hours to facilitate the comprehensive absorption of the lubricant by the polytetrafluoroethylene micropowder, so that the two can be fully mixed to make the prefabricated material required for processing.
[0047] Put the prefabricated material into the pre-pressing machine for pre-compression, the pressure is 0.5MPa, the pressing temperature is 20 ℃, and the prefabricated molding material is made; then the prefabricated molded product is put into the pusher for pressing, the pressing temperature is 160 ℃, the pressure is 3.5MPa, and then made into a columnar mold material.
[0048] The cylindrical mold material is cal...
Embodiment 2
[0054] Mix the polytetrafluoroethylene micropowder and aviation kerosene in a weight ratio of 81:19; stir the mixed raw materials at a stirring speed of 4r / min, a stirring temperature of 25°C, and a stirring time of 100min, so that the raw materials are fully mixed.
[0055] Place the stirred mixed raw materials at a temperature of 50°C for 50 hours to facilitate the comprehensive absorption of the lubricant by the polytetrafluoroethylene micropowder, so that the two can be fully mixed to make the prefabricated material required for processing.
[0056] Put the prefabricated material into the pre-pressing machine for pre-compression, the pressure is 0.6MPa, the pressing temperature is 25°C, and the prefabricated molding material is made; then the prefabricated molding is put into the pusher for pressing, the pressing temperature is 170°C, and the pressure is 3.8MPa, and then made into a columnar mold material.
[0057] The cylindrical mold material is calendered and pressed in...
Embodiment 3
[0063] Mix polytetrafluoroethylene micropowder and aviation kerosene at a weight ratio of 21:4; stir the mixed raw materials at a stirring speed of 5 r / min, a stirring temperature of 30°C, and a stirring time of 120 min, so that the raw materials are fully mixed.
[0064] Place the stirred mixed raw materials at a temperature of 60°C for 60 hours to facilitate the comprehensive absorption of the lubricant by the polytetrafluoroethylene micropowder, so that the two can be fully mixed to make the prefabricated material required for processing.
[0065] Put the prefabricated material into the pre-pressing machine for pre-compression, the pressure is 0.8MPa, the pressing temperature is 30°C, and the prefabricated molding material is made; then the prefabricated molded product is put into the pusher for pressing, the pressing temperature is 180°C, and the pressure is 4.2MPa, and then made into a columnar mold material.
[0066] The cylindrical molding material is calendered and pre...
PUM
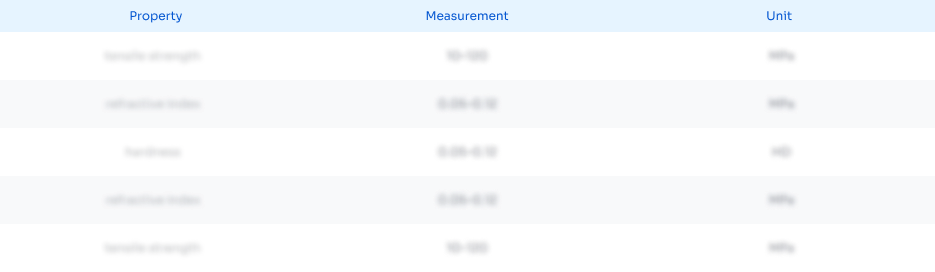
Abstract
Description
Claims
Application Information

- R&D
- Intellectual Property
- Life Sciences
- Materials
- Tech Scout
- Unparalleled Data Quality
- Higher Quality Content
- 60% Fewer Hallucinations
Browse by: Latest US Patents, China's latest patents, Technical Efficacy Thesaurus, Application Domain, Technology Topic, Popular Technical Reports.
© 2025 PatSnap. All rights reserved.Legal|Privacy policy|Modern Slavery Act Transparency Statement|Sitemap|About US| Contact US: help@patsnap.com