Method for preparing aluminum-copper alloy microarc oxidation film
An aluminum-copper alloy, micro-arc oxidation technology, applied in the direction of anodic oxidation, etc., can solve the problems of burning parts, restricting the application of aluminum-copper alloy, and many defects in the oxide film layer, and achieves easy proportioning, easy operation and control, and rich sources Effect
- Summary
- Abstract
- Description
- Claims
- Application Information
AI Technical Summary
Problems solved by technology
Method used
Image
Examples
Embodiment 1
[0017] In this example, the test material is cast aluminum-copper alloy ZL201, according to the process flow figure 1 Prepare the micro-arc oxidation film layer, the composition of the electrolyte composition, process parameters and film layer properties are shown in Table 1:
[0018] Table 1. The composition of the electrolyte composition, process parameters and film layer performance comprehensive table
[0019]
[0020] Note: 1. The power supply voltage used in Table 1 is 550V~700V.
[0021] 2. The test temperature is not higher than 35 ℃.
[0022] 3. The corrosion resistance of the film layer is tested according to the experimental standards required by the national standard GB / T 10125-1997 (eqv ISO 9227: 1990) of the People's Republic of China. Continuous spray is used, and the salt spray test period is 96 hours. The grade after assessment implemented by the national standard GB6461-86 of the People's Republic of China.
[0023] 4. The hardness is measured by a Vick...
Embodiment 2
[0025] In this embodiment, the test material is the deformed aluminum-copper alloy 2A14, according to the process flow figure 1 Prepare the micro-arc oxidation film layer, the composition, process parameters and film layer performance of the electrolyte composition are shown in Table 2:
[0026] Table 2. The composition of the electrolyte composition, process parameters and film layer performance comprehensive table
[0027]
[0028] Note: 1. The power supply voltage used in Table 2 is 550V~700V.
[0029] 2. The test temperature is not higher than 35 ℃.
[0030] 3. The corrosion resistance of the film layer is tested according to the experimental standards required by the national standard GB / T 10125-1997 (eqv ISO 9227: 1990) of the People's Republic of China. Continuous spray is used, and the salt spray test period is 96 hours. The grade after assessment implemented by the national standard GB6461-86 of the People's Republic of China.
[0031] 4. The hardness is measure...
PUM
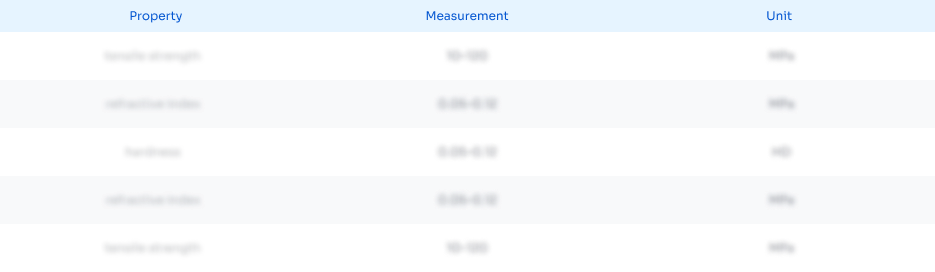
Abstract
Description
Claims
Application Information

- R&D
- Intellectual Property
- Life Sciences
- Materials
- Tech Scout
- Unparalleled Data Quality
- Higher Quality Content
- 60% Fewer Hallucinations
Browse by: Latest US Patents, China's latest patents, Technical Efficacy Thesaurus, Application Domain, Technology Topic, Popular Technical Reports.
© 2025 PatSnap. All rights reserved.Legal|Privacy policy|Modern Slavery Act Transparency Statement|Sitemap|About US| Contact US: help@patsnap.com