Tool and method for repairing composite laminated sheet structural member
A technology for composite material layers and structural parts, which is applied in the direction of manufacturing tools, metal processing equipment, grinding machines, etc., can solve problems such as mismatch between the motherboard and the pre-cured patch, poor repair effect, and inaccurate angles, and achieve improved grinding Improve cutting quality and work efficiency, save repair cost and improve repair strength
- Summary
- Abstract
- Description
- Claims
- Application Information
AI Technical Summary
Problems solved by technology
Method used
Image
Examples
Embodiment 1
[0021] Example 1 as attached Figure 1-4 Shown: a repair tool for an aircraft vertical tail box with a carbon fiber composite laminate structure includes a pair of male grinding wheels 1 and female grinding wheels 2 that match each other with the same dimensions; the male grinding wheel 1 consists of a cam body 11 and a convex diamond particle coating 12 Composition, the cam body 11 is made up of the first drill rod 111, the first cylinder 112 and the outer convex cone 113 which share the same central axis and are connected as one; the outer convex cone 113 is provided with a cylindrical boss 115 sharing the same central axis and located at The first central bottom hole 116 in the inner cavity of the cylindrical boss 115 and the three radially evenly distributed first elongated grooves 114 communicating with the first central bottom hole 116; the outer convex surface 117 of the outer convex cone 113 is coated with convex diamond The particle coating 12, the convex diamond pa...
Embodiment 2
[0022] Example 2: The method for repairing the vertical tail box of an aircraft with a carbon fiber composite material laminate structure using the above tools, including:
[0023] Determine the inner diameter of the first central bottom hole 116 of the male grinding wheel and the outer diameter of the cylindrical boss 115 of the male grinding wheel according to the diameter of the damaged hole contained in the vertical tail box that needs to be repaired, and then according to the cone vertex angle α of the outer convex surface and the composite material layer The thickness of the pressure plate determines the outer diameter of the outer convex cone 113 of the male grinding wheel; the inner diameter of the second center bottom hole 216 of the female grinding wheel is equal to the outer diameter of the cylindrical boss 115 of the male grinding wheel, the apex angle of the inner concave cone β=α, and the inner concave cone 213 The outer diameter of the outer diameter is equa...
PUM
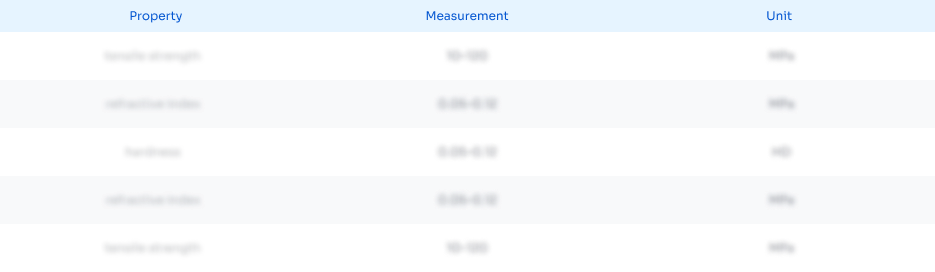
Abstract
Description
Claims
Application Information

- R&D Engineer
- R&D Manager
- IP Professional
- Industry Leading Data Capabilities
- Powerful AI technology
- Patent DNA Extraction
Browse by: Latest US Patents, China's latest patents, Technical Efficacy Thesaurus, Application Domain, Technology Topic, Popular Technical Reports.
© 2024 PatSnap. All rights reserved.Legal|Privacy policy|Modern Slavery Act Transparency Statement|Sitemap|About US| Contact US: help@patsnap.com