Surface-coated cutting tool
A cutting tool and surface coating technology, which is applied in the field of surface coating cutting tools made of cubic crystal boron nitride-based ultra-high pressure sintered materials, can solve the problems of short service life, insufficient adhesion strength between cBN tool substrate and hard film, and prone to defects and other problems, to achieve the effect of increased adhesion strength, excellent adhesion strength, and excellent wear resistance
- Summary
- Abstract
- Description
- Claims
- Application Information
AI Technical Summary
Problems solved by technology
Method used
Image
Examples
Embodiment Construction
[0037]Hereinafter, the surface-coated cutting tool of the present invention will be described based on examples.
[0038] As raw material powders, cBN powder, TiN powder, AlN powder, TiC powder, TiCN powder, Ti 3 Al powder, Ti 2 Al powder, TiAl 3 powder, Al powder, Al 2 o 3 powder, Co powder, and WC powder, mix these raw material powders with the compounding composition shown in Table 1, wet mix them with a ball mill for 80 hours, dry them, and press them under a pressure of 120MPa to form pressed powders with a size of 50mm in diameter and 1.5mm in thickness Next, the green compact is sintered in a vacuum atmosphere with a pressure of 1Pa and at a specified temperature in the range of 900 to 1300°C for 60 minutes to form a pre-sintered body for cutting blades. The preliminary sintered body is placed in a normal ultra-high pressure sintering device in a state where the prepared sintered body is superimposed on a supporting piece made of WC-based cemented carbide with a dia...
PUM
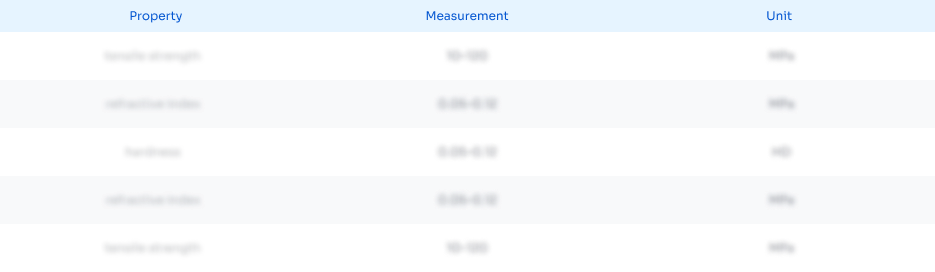
Abstract
Description
Claims
Application Information

- R&D Engineer
- R&D Manager
- IP Professional
- Industry Leading Data Capabilities
- Powerful AI technology
- Patent DNA Extraction
Browse by: Latest US Patents, China's latest patents, Technical Efficacy Thesaurus, Application Domain, Technology Topic, Popular Technical Reports.
© 2024 PatSnap. All rights reserved.Legal|Privacy policy|Modern Slavery Act Transparency Statement|Sitemap|About US| Contact US: help@patsnap.com