Process for smelting and producing medium high carbon steel
A production process, medium and high carbon technology, applied in the direction of manufacturing converters, etc., can solve problems such as insufficient refining processing capacity, and achieve the effect of improving the ability to capture deoxygenation products
- Summary
- Abstract
- Description
- Claims
- Application Information
AI Technical Summary
Problems solved by technology
Method used
Examples
Embodiment 1
[0029] This embodiment is a smelting production process of medium-high carbon steel, and its production process route is: converter smelting-tapping deoxidation alloying--arr blowing station treatment-continuous casting pouring.
[0030] Converter smelting: metal materials are put into the furnace → oxygen is supplied for blowing → lime is added during the blowing process, ore is returned, dolomite slag is made → the end point P and S meet the requirements of the smelted steel type → steel is tapped from the converter to the ladle.
[0031] The deoxidation and alloying sequence of tapping is as follows: at 1 / 10 of the entire tapping time, silicon-aluminum-calcium alloy, low-melting point synthetic slag and alloyed alloys are sequentially added, and at 2 / 3 of the entire tapping time, all alloys are added; The addition amount of silicon-aluminum-calcium alloy is 3Kg / ton of steel; the addition amount of low-melting point synthetic slag is 5Kg / ton of steel;
[0032] The low meltin...
Embodiment 2
[0047] This embodiment is a smelting production process of medium-high carbon steel, and its production process route is: converter smelting-tapping deoxidation alloying-arr blowing station treatment-continuous casting pouring.
[0048] Converter smelting: metal materials are put into the furnace → oxygen is supplied for blowing → lime is added during the blowing process, ore is returned, dolomite slag is made → the end point P and S meet the requirements of the smelted steel type → steel is tapped from the converter to the ladle.
[0049] The deoxidation and alloying sequence of tapping is as follows: at 1 / 10 of the entire tapping time, silicon-aluminum-calcium alloy, low-melting point synthetic slag and alloyed alloys are sequentially added, and at 2 / 3 of the entire tapping time, all alloys are added; The addition amount of silicon-aluminum-calcium alloy is 3.5Kg / ton of steel; the addition amount of low-melting point synthetic slag is 6Kg / ton of steel;
[0050] The low melti...
Embodiment 3
[0066] This embodiment is a smelting production process of medium-high carbon steel, and its production process route is: converter smelting-tapping deoxidation alloying-arr blowing station treatment-continuous casting pouring.
[0067] Converter smelting: metal materials are put into the furnace → oxygen is supplied for blowing → lime is added during the blowing process, ore is returned, dolomite slag is made → the end point P and S meet the requirements of the smelted steel type → steel is tapped from the converter to the ladle.
[0068] The deoxidation and alloying sequence of tapping is as follows: at 1 / 10 of the entire tapping time, silicon-aluminum-calcium alloy, low-melting point synthetic slag and alloyed alloys are sequentially added, and at 2 / 3 of the entire tapping time, all alloys are added; The addition amount of silicon-aluminum-calcium alloy is 4Kg / ton of steel; the addition amount of low melting point synthetic slag is 7Kg / ton of steel;
[0069] Low melting point...
PUM
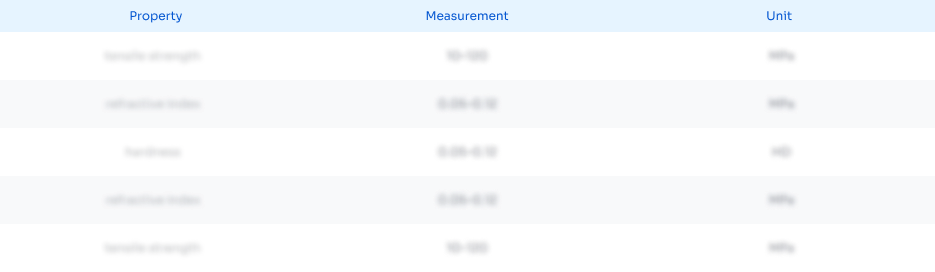
Abstract
Description
Claims
Application Information

- Generate Ideas
- Intellectual Property
- Life Sciences
- Materials
- Tech Scout
- Unparalleled Data Quality
- Higher Quality Content
- 60% Fewer Hallucinations
Browse by: Latest US Patents, China's latest patents, Technical Efficacy Thesaurus, Application Domain, Technology Topic, Popular Technical Reports.
© 2025 PatSnap. All rights reserved.Legal|Privacy policy|Modern Slavery Act Transparency Statement|Sitemap|About US| Contact US: help@patsnap.com