Preparation method of efficient and environment-friendly composite fire retardant
A flame retardant and composite technology, which is applied in chemical instruments and methods, dyeing organosilicon compound treatment, fibrous fillers, etc., can solve the problems of discounting the flame retardant effect of organic flame retardants, and reduce processing performance and physical properties The effect of preventing temperature rise and reducing industrial cost
- Summary
- Abstract
- Description
- Claims
- Application Information
AI Technical Summary
Problems solved by technology
Method used
Examples
Embodiment 1
[0019] Embodiment 1: Prepare composite flame retardant and flame-retardant polyurethane foam according to the following steps:
[0020] (1) Add 5.0kg of commercially available attapulgite of 200 meshes to 150kg of water, add 1g of sodium polyacrylate, stir at high speed in a water bath at 60°C, mix thoroughly for 5 hours, let stand for 40 minutes, take the upper layer of attapulgite suspension, vacuum or vacuum freeze-drying to obtain nano-scale attapulgite;
[0021] (2) Add 1.5kg of nano-scale attapulgite to 30kg of water, add 15g of γ-aminopropyltriethoxysilane, stir at a high speed in a water bath at 30°C, and disperse evenly; then add 0.15kg of nano-sized aluminum hydroxide, 0.075kg of tris (dipropylene glycol) phosphite, fully mixed for 5 hours to obtain a viscous mixture, vacuum or vacuum freeze-dried to obtain a composite flame retardant;
[0022] (3) Mix 100 parts by weight of polyoxypropylene triol and 15 parts of the above composite flame retardant; then add 1 part ...
Embodiment 2
[0024] Embodiment 2: Prepare composite flame retardant and flame-retardant polyurethane foam according to the following steps:
[0025] (1) Add 2.0kg of commercially available attapulgite of 200 meshes to 60kg of water, add 50.2g of sodium hexametaphosphate, stir at high speed in a water bath at 60°C, mix thoroughly for 5 hours, and let it stand for 40 minutes. Take the attapulgite suspension in the upper layer and vacuum Or vacuum freeze-drying to obtain nano-scale attapulgite;
[0026] (2) Add 0.5kg of nano-scale attapulgite to 17.5kg of water, add 15g of γ-aminopropyltriethoxysilane, stir at a high speed in a water bath at 30°C, and disperse evenly; then add 0.25kg of nano-sized magnesium hydroxide, 62.5g of N,N-di(2-hydroxyethyl)aminomethylphosphonic acid diethyl ester, mixed thoroughly for 5 hours to obtain a viscous mixture, vacuum or vacuum freeze-dried to obtain a composite flame retardant;
[0027] (3) Mix 100 parts by weight of polyoxypropylene triol and 15 parts of...
Embodiment 3
[0028] Embodiment 3: Prepare composite flame retardant and flame-retardant polyurethane foam according to the following steps:
[0029] (1) Add 10.0kg of commercially available attapulgite of 200 meshes to 300kg of water, add 0.5kg of sodium silicate, stir at high speed in a 60°C water bath, mix thoroughly for 5 hours, and let stand for 40 minutes. Take the upper layer of attapulgite suspension, vacuum or Vacuum freeze-drying to obtain nano-scale attapulgite;
[0030] (2) Add 2.0kg of nano-scale attapulgite to 100kg of water, add 0.1kg of γ-aminopropyltriethoxysilane, stir at a high speed in a water bath at 30°C, and disperse evenly; then add 0.8kg of nano-sized zinc oxide, 0.4kg N,N-di(2-hydroxyethyl)aminomethylphosphonic acid dimethyl ester, mixed thoroughly for 5 hours to obtain a viscous mixture, vacuum or vacuum freeze-dried to obtain a composite flame retardant;
[0031] (3) Mix 100 parts by weight of polyoxypropylene triol and 15 parts of the above composite flame reta...
PUM
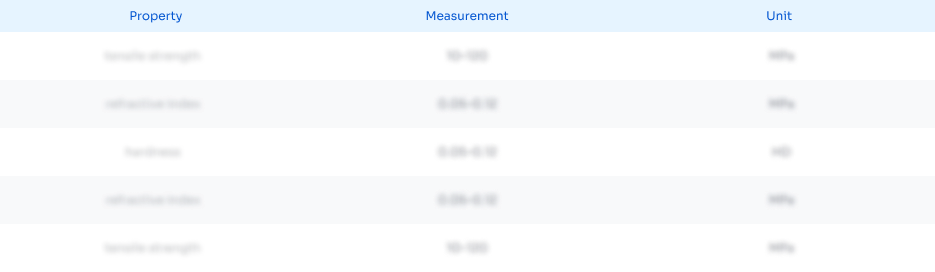
Abstract
Description
Claims
Application Information

- R&D
- Intellectual Property
- Life Sciences
- Materials
- Tech Scout
- Unparalleled Data Quality
- Higher Quality Content
- 60% Fewer Hallucinations
Browse by: Latest US Patents, China's latest patents, Technical Efficacy Thesaurus, Application Domain, Technology Topic, Popular Technical Reports.
© 2025 PatSnap. All rights reserved.Legal|Privacy policy|Modern Slavery Act Transparency Statement|Sitemap|About US| Contact US: help@patsnap.com