Method and device for recovering polyethylene glycol raffinate byproduct from ethylene glycol process
A polyethylene glycol, recovery method technology, applied in chemical instruments and methods, separation/purification of hydroxyl compounds, water/sewage multi-stage treatment, etc., can solve problems such as recovery and utilization of polyethylene glycol residues that have not yet been seen , to shorten the residence time, improve the film forming effect and enhance the heat transfer effect
- Summary
- Abstract
- Description
- Claims
- Application Information
AI Technical Summary
Problems solved by technology
Method used
Image
Examples
Embodiment 1
[0036] A recovery device for polyethylene glycol raffinate, a by-product of the ethylene glycol process, comprising: a preheater, a falling film evaporator, a dehydration rectification tower, an ethylene glycol separation tower, a diethylene glycol separation tower, a triethylene glycol Alcohol separation tower, intermediate tank, centrifuge, one end of the preheater 1 is connected to the falling film evaporator 2, and the top of the falling film evaporator 2 is sequentially connected to the dehydration rectification tower 3, the ethylene glycol separation tower 4, the diethylene glycol separation tower The glycol separation tower 5 and the triethylene glycol separation tower 6 are connected; the bottom of the falling film evaporator 2 is connected with the intermediate tank 7, the centrifuge 8, and the other end of the preheater 1 successively; the falling film evaporator 2 is a scraper type falling film evaporator.
[0037]Add 2% industrial-grade phosphoric acid (85%) to the...
Embodiment 2
[0040] Add 1% industrial-grade phosphoric acid (85%) to the raw material polyethylene glycol waste liquid, adjust the pH value to 9, transport it into the preheater 1 through a pump, preheat it to 200°C, and then transport it to the scraper type with an operating pressure of 30KPa Falling film evaporator 2, heavy components and salts are obtained from the bottom of the evaporator, and the heavy components are separated by a centrifuge 8 and circulated into the preheater 1; the polyol mixed liquid and water obtained from the top of the evaporator are sent to the dehydration distillation tower 3. The operating pressure of the dehydration distillation tower is 40KPa, the temperature at the top of the tower is 70°C, and the temperature at the bottom of the tower is 200°C. The ethylene glycol product is obtained at the top of the ethylene glycol separation tower 4 with an operating pressure of 40KPa, a tower top temperature of 175°C, and a bottom temperature of 220°C, and the mixed ...
Embodiment 3
[0043] Add 4% industrial-grade phosphoric acid (85%) to the raw material polyethylene glycol waste liquid, adjust the pH value to 7, transport it into the preheater 1 through a pump, preheat it to 220°C, and then transport it to the scraper type with an operating pressure of 40KPa Falling film evaporator 2, heavy components and salts are obtained from the bottom of the evaporator, and the heavy components are separated by a centrifuge and circulated into the preheater 1; the polyol mixed liquid and water obtained from the top of the evaporator are sent to the dehydration distillation tower 3. The operating pressure of the dehydration distillation tower is 30KPa, the temperature at the top of the tower is 65°C, and the temperature at the bottom of the tower is 200°C. The ethylene glycol product is obtained at the top of the ethylene glycol separation tower 4 with an operating pressure of 30KPa, a tower top temperature of 155°C, and a bottom temperature of 200°C, and the mixed al...
PUM
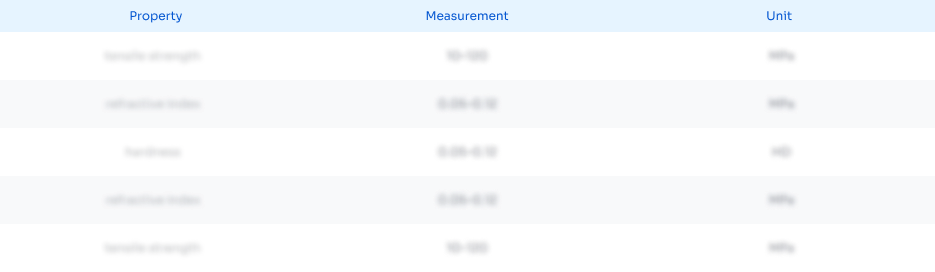
Abstract
Description
Claims
Application Information

- R&D
- Intellectual Property
- Life Sciences
- Materials
- Tech Scout
- Unparalleled Data Quality
- Higher Quality Content
- 60% Fewer Hallucinations
Browse by: Latest US Patents, China's latest patents, Technical Efficacy Thesaurus, Application Domain, Technology Topic, Popular Technical Reports.
© 2025 PatSnap. All rights reserved.Legal|Privacy policy|Modern Slavery Act Transparency Statement|Sitemap|About US| Contact US: help@patsnap.com