Method for comprehensively recovering valuable metals from low-grade tellurium slag
A valuable metal, low-grade technology, used in non-metallic elements, selenium/tellurium compounds, chemical instruments and methods, etc., can solve the problems of prolonged metal recovery period, large metal loss, low tellurium leaching rate, etc. The effect of operability, reducing the amount of slag returned, and improving the direct yield
- Summary
- Abstract
- Description
- Claims
- Application Information
AI Technical Summary
Problems solved by technology
Method used
Image
Examples
example 1
[0035] Take 200g of low-grade tellurium slag containing Te4.41%, Cu9.41%, Sb8.93%, and Bi34.09%, and grind it to a particle size of 100% below 80 mesh. Ratio of 7:1, stirring speed 150r / min under the conditions of leaching 2hr filtration, sulfuric acid leaching solution 1.5L, containing Cu11.91g / L, Te0.3g / L, acid leaching residue after drying weighed 158g, its composition (% ): Contains Te5.16, Cu0.96, Sb12.67, Bi41.88, Cu leaching rate is 93.4% during sulfuric acid leaching. Copper is recovered from sulfuric acid leaching solution by conventional methods.
[0036] Sulfuric acid leaching residue 100g, after leaching for 4 hours under the conditions of volume 600mL, hydrochloric acid concentration 6mol / L, temperature 85°C, stirring speed 150r / min, cool to room temperature and filter, hydrochloric acid leaching solution 710mL, its composition (g / L) Te6.9 . Bi96.9. The leached slag is returned to the converter for smelting.
[0037] Hydrochloric acid leaching solution 650mL, ...
example 2
[0041] Take 200g of low-grade tellurium slag containing Te6.64%, Cu9.64%, Sb9.71%, and Bi27.69%, and grind it to a particle size of 100% or less than 80 mesh. The ratio was 7:1, the stirring speed was 150r / min, leached for 1.5hr and filtered, the sulfuric acid immersion solution was 1.36L, containing Cu13.61g / L, and the acid leaching residue was weighed 151.2g after drying, and its composition (%): containing Te8.58, Sb12.49, Bi35.89, Cu leaching rate is 96% during sulfuric acid leaching. Copper is recovered from the sulfuric acid leaching solution, and the sulfuric acid leaching residue is carried out to the next process.
[0042] Sulfuric acid leaching residue 100g, after leaching for 4 hours under the conditions of volume 600mL, hydrochloric acid concentration 8mol / L, temperature 85°C, stirring speed 150r / min, cool to room temperature and filter, hydrochloric acid leaching solution 610mL, its composition (g / L) Te14. 03. Sb19.57, Bi58.25, acid leaching residue weighed 8g af...
PUM
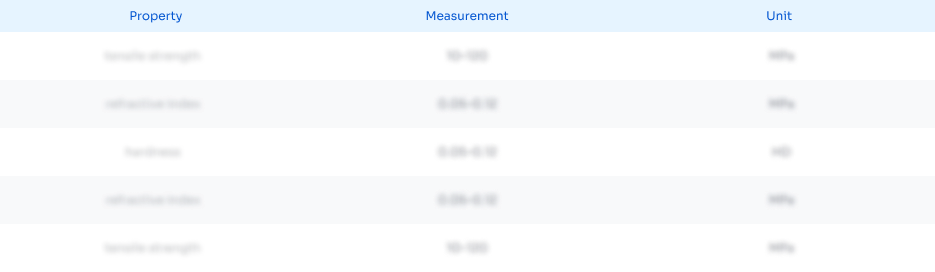
Abstract
Description
Claims
Application Information

- R&D
- Intellectual Property
- Life Sciences
- Materials
- Tech Scout
- Unparalleled Data Quality
- Higher Quality Content
- 60% Fewer Hallucinations
Browse by: Latest US Patents, China's latest patents, Technical Efficacy Thesaurus, Application Domain, Technology Topic, Popular Technical Reports.
© 2025 PatSnap. All rights reserved.Legal|Privacy policy|Modern Slavery Act Transparency Statement|Sitemap|About US| Contact US: help@patsnap.com