Method for measuring geometric error parameter value of rotary oscillation axis of five-axis linkage numerical control machine tool
A CNC machine tool, rotary swing technology, used in measuring/indicating equipment, metal processing mechanical parts, metal processing equipment, etc., can solve problems such as lack of geometric error parameters
- Summary
- Abstract
- Description
- Claims
- Application Information
AI Technical Summary
Problems solved by technology
Method used
Image
Examples
Embodiment
[0117] Taking the swing axis of workbench A of an A'C' type five-axis high-speed machining center as an example, the error test experiment was carried out ( Image 6 shown), the implementation steps are as follows:
[0118] (1) Install the ballbar and measuring accessories;
[0119] (2) Prepare the measurement program, the test range is -32°~32° on the A axis, keep the C axis at 0°, and stop for 10 seconds to read every 3°;
[0120] (3) Measurement mode 1:
[0121] Pick = =80mm, = =55.694mm, the length of the ballbar is 101.5mm, measure in the X, Y, and Z directions respectively, and record the change of the length of the ballbar , , ;
[0122] (4) Measurement mode 2:
[0123] Pick = =160mm, = =55.694mm, the same as step (3), measure the displacement error in the X, Y, and Z directions again , , ;
[0124] (5) Measurement mode three:
[0125] Pick = =160mm, = =155.694mm, measure the displacement error in the X, Y, and Z directions again...
PUM
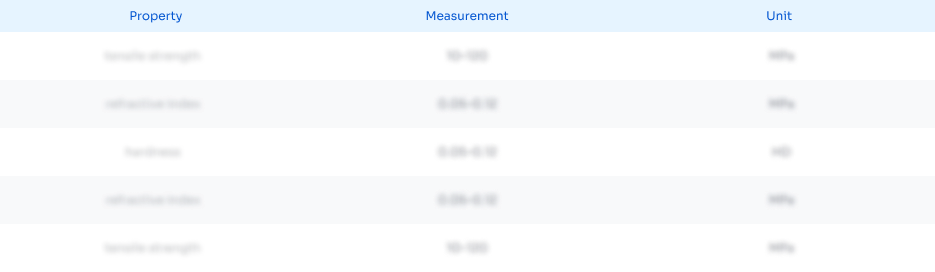
Abstract
Description
Claims
Application Information

- R&D
- Intellectual Property
- Life Sciences
- Materials
- Tech Scout
- Unparalleled Data Quality
- Higher Quality Content
- 60% Fewer Hallucinations
Browse by: Latest US Patents, China's latest patents, Technical Efficacy Thesaurus, Application Domain, Technology Topic, Popular Technical Reports.
© 2025 PatSnap. All rights reserved.Legal|Privacy policy|Modern Slavery Act Transparency Statement|Sitemap|About US| Contact US: help@patsnap.com