Cold deformation recrystallization course-based process method for producing metal composite material
The technology of a metal composite material and a process method is applied in the technical field of producing metal composite materials based on the cold deformation recrystallization process, which can solve the problems of strong impact, smoke and pollution, and achieve the effect of improving the quality and the yield of finished products.
- Summary
- Abstract
- Description
- Claims
- Application Information
AI Technical Summary
Problems solved by technology
Method used
Image
Examples
Embodiment 1
[0024] A 10mm thick stainless steel plate is combined with a 30mm thick Q235 steel plate. Firstly, one surface of the two metal materials is respectively processed by a milling machine to obtain a flat and smooth surface, and the degree of work hardening is about 100%.
[0025] After cleaning the two processed surfaces, press the hardened surfaces of the two materials against each other and closely overlap them, and press them on the press with a unit pressure of 0.3 ~ 2Mpa or press them at a pressure of 0.5Pa ~ 1X10 -2 Weld and seal the peripheral joints under the vacuum state of pa; heat the material, gradually heating to above 650°C, keep it warm for about 1 hour, then cool slowly, and the two materials are combined into one. The same method can be used to obtain a double-sided composite material in which the middle layer is plain carbon steel and the upper and lower layers are stainless steel.
Embodiment 2
[0027] Composite two 200mm thickness Q235 continuous casting billets. Firstly, one surface of the two steel billets is machined with a milling machine to obtain a flat and clean surface, and the degree of work hardening is about 100%.
[0028] After purging and cleaning the two processing surfaces, press the two material processing hardening surfaces relatively close together, and press them with a unit pressure of 0.3 ~ 2Mpa or 0.5Pa ~ 1X10 -2 Welding and sealing the peripheral joints under the vacuum state of Pa;
[0029] The material is heated, gradually heated to above 650°C, kept warm for about 2 hours, then cooled slowly, and the opposite surfaces of the two materials are combined into one. It is used as an extra-thick slab material for hot-rolled steel plates. It can also be heated at 650°C after the two materials have been compounded into one, and continue to be heated to the temperature required for rolling, and are directly used for rolling to produce steel plates....
PUM
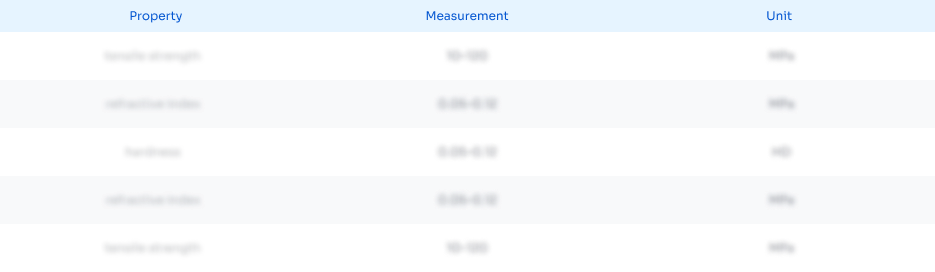
Abstract
Description
Claims
Application Information

- R&D
- Intellectual Property
- Life Sciences
- Materials
- Tech Scout
- Unparalleled Data Quality
- Higher Quality Content
- 60% Fewer Hallucinations
Browse by: Latest US Patents, China's latest patents, Technical Efficacy Thesaurus, Application Domain, Technology Topic, Popular Technical Reports.
© 2025 PatSnap. All rights reserved.Legal|Privacy policy|Modern Slavery Act Transparency Statement|Sitemap|About US| Contact US: help@patsnap.com