Method for making package materials from straws
A packaging material and straw technology, which is applied in manufacturing tools, wood processing equipment, reed/straw processing, etc., can solve the problems of environmental pollution and high manufacturing cost, and achieve the effect of reducing energy consumption and improving pulp quality
- Summary
- Abstract
- Description
- Claims
- Application Information
AI Technical Summary
Problems solved by technology
Method used
Image
Examples
Embodiment 1
[0024] In this embodiment, corn stalks are used as the main raw material, and sodium hydroxide is used as the activator, and the sodium hydroxide accounts for 9.0% of the mass of the dry stalks. The corn stalks are separated from the husks and husks with a corn stalk husk and husk separator, and the outer husks of the corn stalks are crushed to a length of 3 cm, and air-dried to a moisture content of about 10%. When pre-soaking at room temperature at 25°C, the concentration of sodium hydroxide is 1.5%, the solid-liquid ratio is 1:6, and the pre-soaking is for 2 hours; after pre-soaking, filter out 50% of the water, and steam for 45 minutes at 100°C; The final straw is filtered with a filter press, and the waste liquid is reused as the presoak liquid for the next round of activation; after that, the straw is washed and filtered for 3-4 times, and the washing liquid is collected separately. - 2 washes as presoak for next round of activation, 3-4 washes as next round of washes. ...
Embodiment 2
[0026] In this embodiment, corn stalks are used as the main raw material, and sodium hydroxide is used as the activator, and the sodium hydroxide accounts for 12.0% of the dry straw mass. Corn stalks are crushed to a length of 4 cm. When presoaked at room temperature, the concentration of sodium hydroxide is 1.7%, the solid-to-liquid ratio is 1:7, and presoaked for 2 hours; after presoaking, filter out 50% of the water and steam at 100 ° C Raise for 1 hour; the steamed straw is filtered with a filter press, and the waste liquid is reused as the presoak liquid for the next round of activation; after that, the straw is washed and filtered for 3-4 times, washing The liquids were collected separately, the 1st-2nd washing liquid was used as the presoak liquid for the next round of activation, and the 3rd-4th washing liquid was used as the next round of washing liquid. The straw after chemical pretreatment is ground with a high-concentration disc mill; the ground pulp is formed on a...
Embodiment 3
[0028]In this embodiment, corn stalks are used as the main raw material, potassium hydroxide is used as an activator, and potassium hydroxide accounts for 9.0% of the dry straw mass. Corn stalks are crushed to a length of 4 cm. When presoaked at room temperature, the concentration of sodium hydroxide is 1.5%, the solid-to-liquid ratio is 1:6, and presoaked for 2 hours; after presoaking, filter out 50% of the water and steam at 100 ° C Raise for 1 hour; the steamed straw is filtered with a filter press, and the waste liquid is reused as the pre-soaking for the next round of activation; after that, the straw is washed and filtered for 3-4 times, and the washing liquid Collected separately, the 1st-2nd washing solution is used as the presoak solution for the next round of activation, and the 3rd-4th washing solution is used as the next round of washing solution. The straw after chemical pretreatment is ground with a high-concentration disc mill; the ground pulp is formed on a pap...
PUM
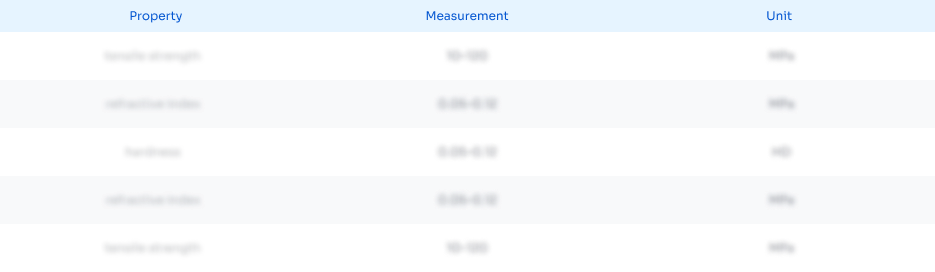
Abstract
Description
Claims
Application Information

- R&D Engineer
- R&D Manager
- IP Professional
- Industry Leading Data Capabilities
- Powerful AI technology
- Patent DNA Extraction
Browse by: Latest US Patents, China's latest patents, Technical Efficacy Thesaurus, Application Domain, Technology Topic, Popular Technical Reports.
© 2024 PatSnap. All rights reserved.Legal|Privacy policy|Modern Slavery Act Transparency Statement|Sitemap|About US| Contact US: help@patsnap.com