Aluminum alloy material with high bake hardening capability for 6-series automobile bodies
A technology of aluminum alloy material and automobile body, which is applied in the field of 6 series aluminum alloy and 6xxx series high bake hardenable aluminum alloy material for automobile body, which can solve the problems of high Cu content, low bake hardenability and high yield strength
- Summary
- Abstract
- Description
- Claims
- Application Information
AI Technical Summary
Problems solved by technology
Method used
Image
Examples
Embodiment 1
[0021] The composition of the aluminum alloy is calculated by mass percentage: Si 0.50wt%, Mg 0.60wt%, Mn 0.20wt%, Fe 0.05wt%, Cu 0.30wt%, Ti 0.15wt%, Cr 0.10wt%, and the balance is Al. After the aluminum alloy ingot is homogenized, it is hot-rolled and cold-rolled to a thin plate of 1mm; the thin plate is water-quenched after solution treatment, and after two weeks of natural aging, it is simulated stamping and baked (2% pre-deformation + 175℃×30min) .
Embodiment 2
[0023] The composition of the aluminum alloy is calculated by mass percentage: Si 0.60wt%, Mg 1.30wt%, Mn 0.18wt%, Fe 0.25wt%, Cu 0.01wt%, Ti 0.10wt%, Cr 0.08wt%, and the balance is Al. After the aluminum alloy ingot is homogenized, it is hot-rolled and cold-rolled to a thin plate of 1mm; the thin plate is water-quenched after solution treatment, and after two weeks of natural aging, it is simulated stamping and baked (2% pre-deformation + 175℃×30min) .
Embodiment 3
[0025] The composition of the aluminum alloy is calculated by mass percentage: Si 1.00wt%, Mg 0.60wt%, Mn 0.05wt%, Fe 0.05wt%, Cu 0.20wt%, Ti 0.15wt%, Cr 0.10wt%, and the balance is Al. After the aluminum alloy ingot is homogenized, it is hot-rolled and cold-rolled to a thin plate of 1mm; the thin plate is water-quenched after solution treatment, and after two weeks of natural aging, it is simulated stamping and baked (2% pre-deformation + 175℃×30min) .
PUM
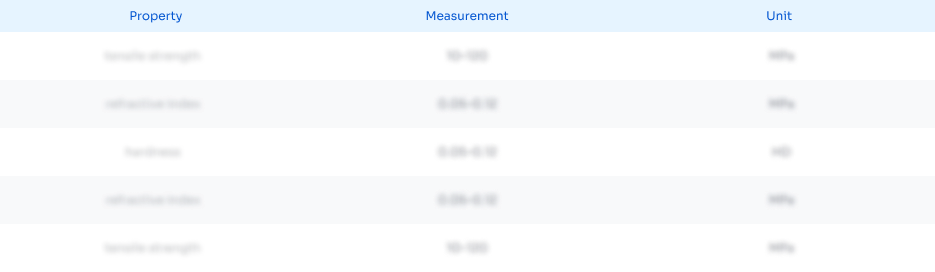
Abstract
Description
Claims
Application Information

- R&D Engineer
- R&D Manager
- IP Professional
- Industry Leading Data Capabilities
- Powerful AI technology
- Patent DNA Extraction
Browse by: Latest US Patents, China's latest patents, Technical Efficacy Thesaurus, Application Domain, Technology Topic, Popular Technical Reports.
© 2024 PatSnap. All rights reserved.Legal|Privacy policy|Modern Slavery Act Transparency Statement|Sitemap|About US| Contact US: help@patsnap.com