Heat treatment process for ASDO clamp products
A process and product technology, applied in the field of heat treatment process of ASDO cable clamp products, can solve the problems of unsatisfactory requirements, low Charpy impact value, substandard mechanical properties, etc., to eliminate internal stress, ensure hardenability, and prevent distortion Effect
- Summary
- Abstract
- Description
- Claims
- Application Information
AI Technical Summary
Problems solved by technology
Method used
Image
Examples
Embodiment 1
[0016] Embodiment 1: According to the following steps to produce M100 clamp
[0017] (1) Normalizing treatment: first heat the workpiece to 860±10°C for 2 hours, then take it out of the furnace and cool it to room temperature;
[0018] (2) Quenching treatment: firstly, heat the workpiece after the above normalizing treatment to 700±10°C for 3 hours; then, continue to heat up to 930±10°C for 4 hours; Quenching in 10% PQG quenching liquid for 10 minutes; finally, the quenched workpiece is cooled to 200°C in the water cooling pool and dried for a while;
[0019] (3) Tempering treatment: First, the workpiece after the above quenching treatment is heated to 450±10°C for 1 hour; then, the temperature is raised to 630±10°C for 7 hours; finally, it is air-cooled to 500°C, and then The water-cooled pool is cooled to 200°C to discharge water and cooled to room temperature.
Embodiment 2
[0020] Embodiment 2: According to the following steps to produce M110 clamp
[0021] (1) Normalizing treatment: first heat the workpiece to 860±10°C for 2.5 hours, then take it out of the furnace and cool it to room temperature;
[0022] (2) Quenching treatment: First, the workpiece after the above normalizing treatment is heated to 700±10°C for 3.5 hours; then, continue to heat up to 930±10°C for 4.5 hours; then, out of the furnace at a temperature ≤ 38°C mass concentration Quenching in 11% PQG quenching liquid for 15 minutes; finally, the quenched workpiece is cooled to 250°C in the water cooling pool and dried for a while;
[0023] (3) Tempering treatment: First, the workpiece after the above quenching treatment is heated to 450±10°C for 1.5 hours; then, the temperature is raised to 630±10°C for 8 hours; finally, it is air-cooled to 500°C, and then The water cooling pool is cooled to 250°C to discharge water and cooled to room temperature.
Embodiment 3
[0024] Embodiment 3: According to the following steps to produce M120 clamp
[0025] (1) Normalizing treatment: first heat the workpiece to 860±10°C for 3 hours, then take it out of the furnace and cool it to room temperature;
[0026] (2) Quenching treatment: First, the workpiece after the above normalizing treatment is heated to 700±10°C for 4 hours; then, continue to heat up to 930±10°C for 5 hours; then, out of the furnace at a temperature ≤38°C Quenching in 12% PQG quenching liquid for 20 minutes; finally, the quenched workpiece is cooled to 300°C in the water cooling pool and dried for a while;
[0027] (3) Tempering treatment: First, the workpiece after the above quenching treatment is heated to 450±10°C for 2 hours; then, the temperature is raised to 630±10°C for 9 hours; finally, it is air-cooled to 500°C, and then The water-cooled pool is cooled to 300°C to discharge water and cooled to room temperature.
PUM
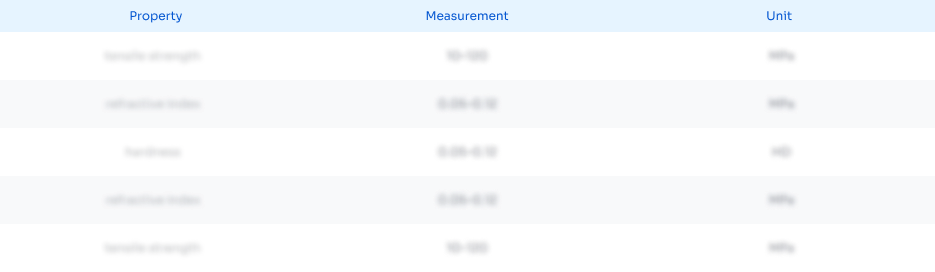
Abstract
Description
Claims
Application Information

- R&D
- Intellectual Property
- Life Sciences
- Materials
- Tech Scout
- Unparalleled Data Quality
- Higher Quality Content
- 60% Fewer Hallucinations
Browse by: Latest US Patents, China's latest patents, Technical Efficacy Thesaurus, Application Domain, Technology Topic, Popular Technical Reports.
© 2025 PatSnap. All rights reserved.Legal|Privacy policy|Modern Slavery Act Transparency Statement|Sitemap|About US| Contact US: help@patsnap.com