Repair welding method and welding tool of stirring friction plug for friction preheating of telescopic shaft shoulder
A friction stir, telescopic shaft technology, applied in welding equipment, manufacturing tools, non-electric welding equipment, etc., can solve the problems of poor continuous fluidity of materials, poor mechanical properties of welded joints, fractures, etc. The effect of improving mechanical properties and simplifying repair welding process
- Summary
- Abstract
- Description
- Claims
- Application Information
AI Technical Summary
Problems solved by technology
Method used
Image
Examples
specific Embodiment approach 1
[0018] Specific implementation mode one: combine figure 1 , Figure 5 , Image 6 with Figure 7 Describe this embodiment, this embodiment is realized through the following steps: 1. The selection of the material of the stirring needle: the material of the stirring needle 3-1 is the same as that of the parts to be repaired; 2. Open the cone-shaped defect repair preset hole: Make a positioning hole at the weld defect to be repaired, and use a type drill to expand the positioning hole into a tapered hole according to the repair welding requirements. The tapered hole is the pre-set hole for repairing the tapered defect to be repaired; Needle size: the external contour dimension of the stirring needle 3-1 should be larger than the internal contour dimension of the conical defect repairing preset hole, so as to ensure sufficient friction and sufficient filling volume between the stirring needle and the defect repairing preset hole; 4. Conical defect repair preset hole positioning...
specific Embodiment approach 2
[0019] Specific implementation mode two: combination Figure 1 ~ Figure 4Describe this embodiment, this embodiment comprises welding tool holding body 1, telescopic shoulder 2, stirring body 3, spring 4, four limit plates 5 and at least four keys 6, and stirring body 3 is formed by stirring needle 3-1 It is composed of the stirring needle handle 3-2, the stirring needle handle 3-2 and the stirring needle 3-1 are integrated from top to bottom, and the outer surface of the stirring needle handle 3-2 is provided with a stirring needle clamping surface 3-2- 1. The stirring needle 3-1 is a cone, and the welding tool holder 1 is composed of a coaxial upper cylinder 1-1 and a lower cylinder 1-2, and the diameter of the upper cylinder 1-1 is smaller than that of the lower cylinder 1- 2, the upper cylinder 1-1 and the lower cylinder 1-2 are integrated, the outer surface of the upper cylinder 1-1 is provided with a welding tool clamping surface 1-1-1, and the lower cylinder 1-2 There i...
specific Embodiment approach 3
[0020] Specific implementation mode three: combination figure 1 To illustrate this embodiment, the lower end surface of the lower ring 2-2 of this embodiment is provided with a concave shoulder surface 2-2-1 whose outer edge is higher than the center. The concave shoulder surface 2-2-1 effectively prevents the material plasticized by the stirring needle 3-1 from flowing out. Other components and connections are the same as those in the second embodiment.
PUM
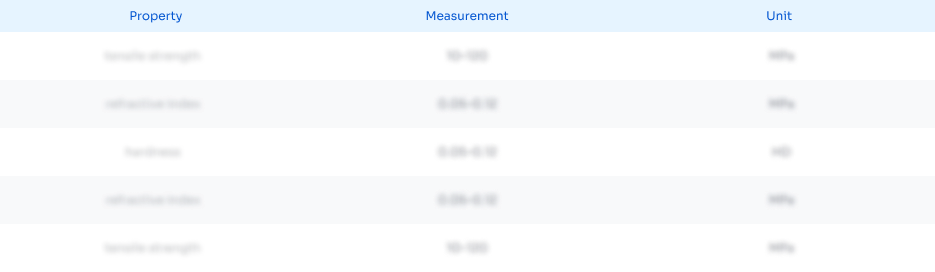
Abstract
Description
Claims
Application Information

- R&D
- Intellectual Property
- Life Sciences
- Materials
- Tech Scout
- Unparalleled Data Quality
- Higher Quality Content
- 60% Fewer Hallucinations
Browse by: Latest US Patents, China's latest patents, Technical Efficacy Thesaurus, Application Domain, Technology Topic, Popular Technical Reports.
© 2025 PatSnap. All rights reserved.Legal|Privacy policy|Modern Slavery Act Transparency Statement|Sitemap|About US| Contact US: help@patsnap.com