Heating method for controlling decarburization in heavy rail billet furnace
A heating method and billet technology, applied in furnaces, heat treatment furnaces, manufacturing tools, etc., can solve the problems of increased oxidative burning loss of steel billets or ingots, increased production costs, labor intensity, and not very obvious application results, and achieves low production costs. The effect of high furnace energy utilization and reduction of pollutant emissions
- Summary
- Abstract
- Description
- Claims
- Application Information
AI Technical Summary
Problems solved by technology
Method used
Examples
Embodiment 1
[0021] When producing 50Kg / m grade U71Mn high-speed heavy rail (carbon content 0.68-0.74%), the rolling line method flow is: continuous casting slab raw material weighing → heating in the regenerative walking beam heating furnace → high pressure water descaling → BD1 blanking→BD2 special-shaped rolling→UEU tandem universal rolling→thermal printing→hot saw cutting head→stepping cooling bed cooling. The bloom (section size 380×280mm) coming from the continuous casting machine is heated in the regenerative walking beam heating furnace. Firstly, the heated steel billets are placed horizontally and loaded into the furnace, the wide side (where the side is 380mm) is horizontal, the narrow side (where the side is 280mm) is vertical, and the steel billets in the furnace are arranged with the minimum distance. Because the distribution of the decarburized layer on the surface of the billet is not evenly distributed during the heating process in the furnace, but shows a tendency that the...
Embodiment 2
[0024] During the heating process of the billet, the whole furnace maintains a positive pressure, and the furnace pressure measuring point is arranged in the middle of the furnace roof in the preheating section, and the furnace pressure control value is kept between 10-30Pa. The atmosphere in the furnace is adjusted by controlling the total air consumption coefficient of the whole furnace, and the control value is kept between 1.0-1.05. The section (when the billet temperature is ≥1000°C) is in a weakly reducing atmosphere, and the air consumption coefficient is controlled at about 1.0. The measured oxygen content of the comprehensive atmosphere in the furnace is between 0-2%. This atmosphere state ensures that the depth of the decarburization layer on the surface of the heated billet is controlled within the shallowest range, and at the same time ensures the complete combustion of fuel and improves energy utilization. and reduce pollutant emissions. During the heating proces...
Embodiment 3
[0026]During the heating process of the billet, the whole furnace maintains a positive pressure, and the furnace pressure measuring point is arranged in the middle of the furnace roof in the preheating section, and the furnace pressure control value is kept between 10-30Pa. The atmosphere in the furnace is adjusted by controlling the total air consumption coefficient of the whole furnace. The control value is kept between 1.0-1.05. The section (when the billet temperature is ≥1000°C) is under a weakly reducing atmosphere, and the air consumption coefficient is controlled at about 0.95. The measured oxygen content of the comprehensive atmosphere in the furnace is between 0-2%. This atmosphere state ensures that the depth of the decarburization layer on the surface of the heated billet is controlled within the shallowest range, and at the same time ensures the complete combustion of fuel and improves energy utilization. and reduce pollutant emissions. During the heating process...
PUM
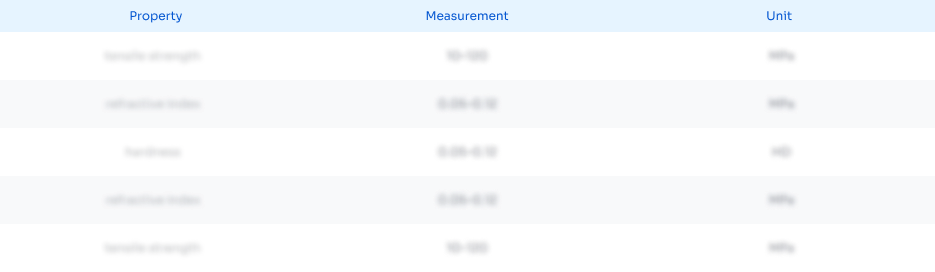
Abstract
Description
Claims
Application Information

- R&D
- Intellectual Property
- Life Sciences
- Materials
- Tech Scout
- Unparalleled Data Quality
- Higher Quality Content
- 60% Fewer Hallucinations
Browse by: Latest US Patents, China's latest patents, Technical Efficacy Thesaurus, Application Domain, Technology Topic, Popular Technical Reports.
© 2025 PatSnap. All rights reserved.Legal|Privacy policy|Modern Slavery Act Transparency Statement|Sitemap|About US| Contact US: help@patsnap.com